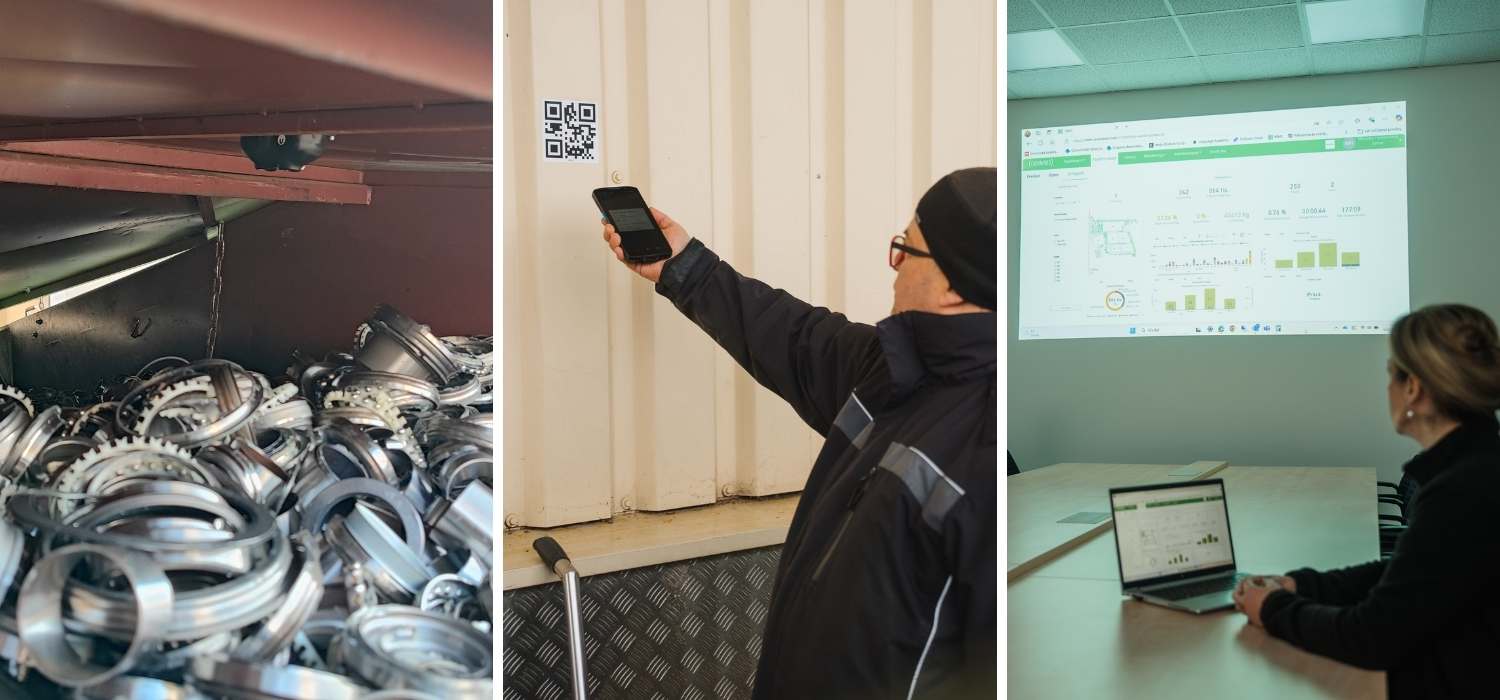
Schaeffler, one of the largest industrial employers in Europe, continues to innovate toward sustainability. As a world-leading Motion Technology Company, it places emphasis not only on production quality but also on the efficient management of environmental processes. The Schaeffler Group views sustainability as a comprehensive, overarching topic and assumes ecological and social responsibility throughout the entire value chain. As part of this strategy, the Schaeffler plant in Skalica, Slovakia has also digitalized its waste management in cooperation with Sensoneo, a leader in smart waste management solutions.
In the summer of 2024, a pilot solution was installed, when the first batch of ultrasonic sensors was deployed into large-capacity containers with 17 different types to monitor their fill levels. The containers have various filling cycles—some, like sheet metal, can accumulate 7 to 10 cubic meters of waste per day, while others, such as aluminum chips, may reach full capacity in as little as a month. During the three-month pilot project, up to 490,000 kg of production waste was recorded in the system.
Data from the sensors is transmitted in real-time via IoT (Internet of Things) technology to the Sensoneo software platform, which can be accessed by both plant operators and the external collection company. As a result, they have an accurate overview of the status of the containers and can arrange for just-in-time collection, eliminating the risk of overfilling. Coordination with the external collection company has improved significantly—rather than exporting half-empty containers, the company now knows in advance which containers and types of waste will need to be collected the next day. The optimization of pickups has also reduced the number of trips and the associated emissions.
However, the system does more than just monitor fill levels. Each container is marked with a QR code that is scanned when it is collected, along with an indication of its weight, which is recorded via a QR code on a weighing slip. The collection vehicle driver uploads this data into the app, completing the entire process of collecting and weighing the waste. This provides operators with accurate data on the weight of the waste in each container at the time of collection. The system also covers types of waste without a fixed container stand, such as scrap pipe material, for which the collection vehicle arrives on call. Additionally, the app allows for the reporting of waste contamination, with the option to attach verification photos. This ensures that the operator does not risk the collection company marking the waste as contaminated without evidence.
Miroslava Hanzlovicova, Head of the Waste Management Team, from Schaeffler, highlighted the main benefits of the solution: “The analytical reports provide us with clear and accurate data in one place, while allowing us to easily filter for a specific period. Real-time monitoring of container status is a major advantage because we can track it remotely, saving time for staff who no longer have to physically check containers or coordinate pickups with the collection company. At the same time, the entire system from Sensoneo is seamlessly connected in an end-to-end way, from measuring container fullness to the final weighing of the waste.”
Another important aspect of this digitization project is that most of the waste types involved are valuable industrial waste that can be further processed, recycled, or sold. Given the positive experience at the Skalica plant, Schaeffler plans to introduce this solution at its other plants in Europe in the near future.
Sensoneo is a global technology company providing innovative solutions for waste management. Through the integration of cutting-edge technology, including robust software and a data-driven approach, Sensoneo enables cities, businesses, and countries to enhance their sustainability performance, optimize waste collection processes, and lower their environmental footprint.
As the only company worldwide, Sensoneo has successfully implemented and operates IT systems for Deposit Return Schemes (DRS) in 8 countries, achieving recycling performance exceeding 90%. With a proven track record across several countries, Sensoneo’s influence in the DRS segment is undeniably growing. Additionally, Sensoneo has designed tools to automate factory waste collection, enabling its customers to improve waste diversion rates and circularity at their locations.
With its team of 140+ professionals, Sensoneo provides complex software and hardware solutions worldwide, with an active presence in Europe, USA, and the MENA region. Sensoneo’s smart waste management solutions have garnered attention from countries, cities, and businesses worldwide, with installations in over 87 countries across five continents. The deployment of smart sensors by Sensoneo is poised to contribute to the largest smart waste installation worldwide, encompassing an impressive 11,100 sensors in Madrid. Notably, Sensoneo holds the distinction of being the first company to implement a narrowband IoT solution in the United States.