This summer, attendees of the Paris Olympics who imbibed at the Cass Pocha outdoor food and drink stall near the Eiffel Tower were offered PLA cups that they could later toss into a special collection bin, thanks to a collaboration between Cass beer, TotalEnergies Corbion and Korean bottler Sansu.
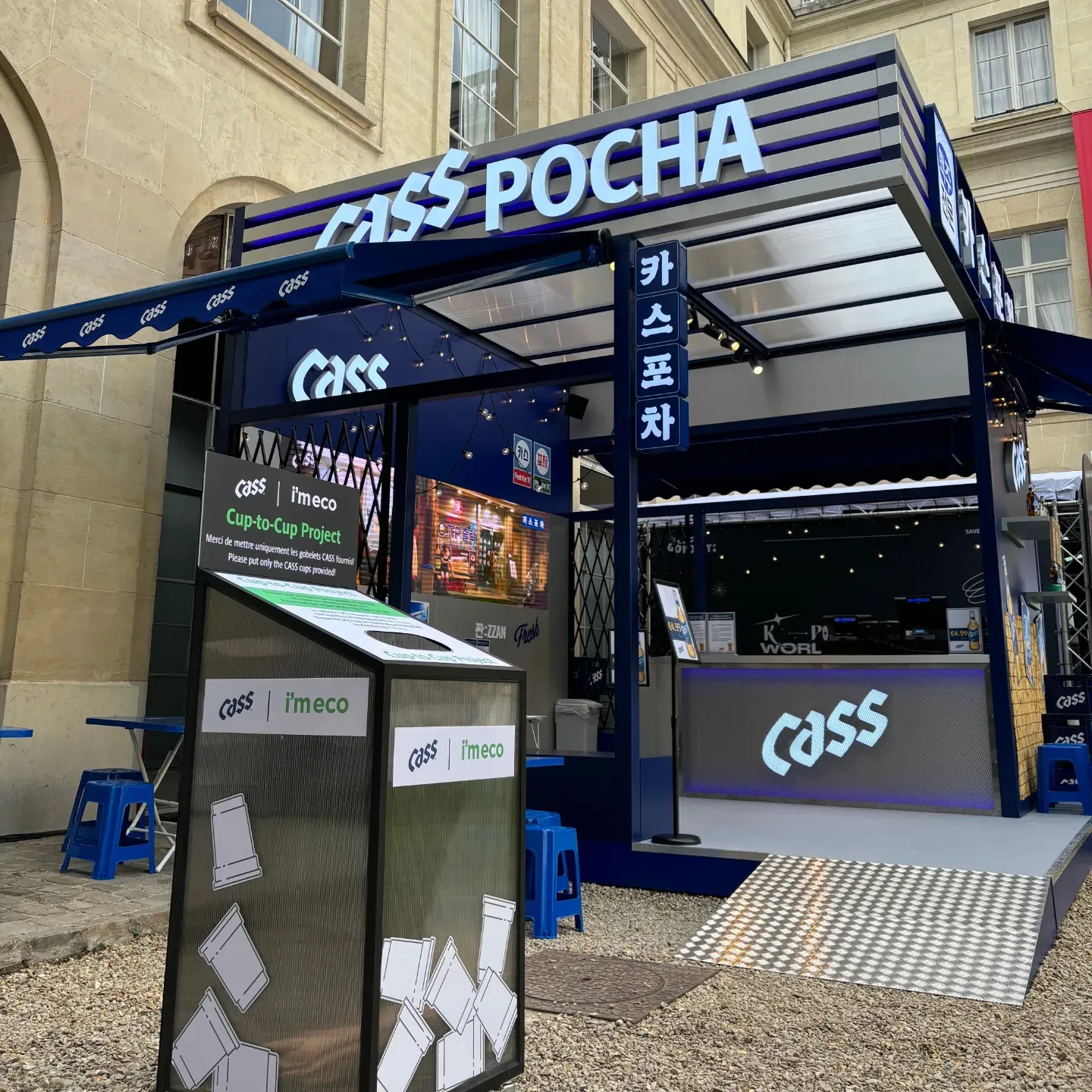
In fact, large sporting events or festivals — especially in cities with policies that ban certain types of plastic packaging — often serve beverages and food in packaging made from polylactic acid.
Single-use packaging is by far the largest end use of PLA, by volume, and demand is growing. The global PLA market as a whole, which also includes agricultural, textile and 3D-printing applications, is expected to see nearly 12% compound annual growth until 2032, when it could exceed $3 billion. But as the PLA packaging market grows, so does the debate over the material’s environmental credentials.
This is largely based on how PLA is marketed; how quickly and fully it biodegrades in composting environments; and its overall suitability for packaging at a time when climate and public health advocates want to see marked declines in single-use plastics.
PLA’s roots
A century ago, when the American chemist and inventor Wallace Carothers rose to prominence at DuPont, material science focused on creating new, synthetic materials. Carothers’ experiments with building long-chain chemicals led to the creation of the synthetic polymers nylon and neoprene, both of which have had a massive impact on society.
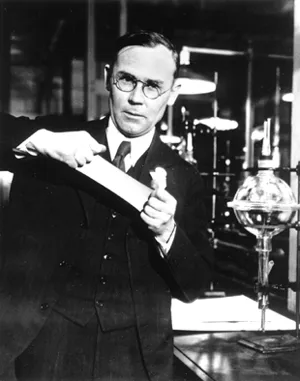
Along the way, Carothers also plasticized a natural resource: lactic acid.
In 1932, he discovered that this chemical, derived from plant starch, could be turned into plastic in the form of PLA. There was no commercial interest in PLA for decades until biomedical engineers found that it works very well for a range of implantable devices, such as stents and sutures. The Food and Drug Administration approved PLA for biomedical uses in the early ‘70s.
Then, in the late ‘80s, agricultural products corporation Cargill started looking at new products that could be derived from the massive amounts of corn it processed each year. Fermenting corn sugar into lactic acid offered a feedstock for PLA, so Cargill chemists began experimenting with ways to turn that lactic acid into PLA on a large scale. In 2002, Cargill opened its PLA plant in Blair, Nebraska, under the name NatureWorks.
“At that time, there was a lot of focus on carbon footprint and the initial thoughts around plastic waste,” said Leah Ford, who until recently served as NatureWorks’ global marketing and communications director.
Plus, she said, there was growing interest in decoupling materials from fossil-based resources because of growing costs. This was before the U.S. hydraulic fracturing boom, which changed the economics considerably. Since then, an increasing share of oil and gas is used in the petrochemical industry and it’s expected to account for half of oil demand by midcentury.
Despite those headwinds, PLA found a foothold in niche packaging applications due to its ability to fully biodegrade in industrial composting facilities.
Today, NatureWorks produces 150,000 metric tons of PLA, called Ingeo, and is owned equally by Cargill and Thai company PTT Global Chemical. It is also building a second plant in Thailand that will produce 75,000 metric tons of PLA from sugarcane annually. That matches the amount of PLA that TotalEnergies Corbion produces in Thailand annually, also from sugarcane. ADM recently canceled plans to build a similarly-size plant in Illinois, citing high construction costs.
Groups such as the nonprofit Clean Production Action consider PLA to be among the more preferable bioplastics available within its GreenScreen certification program that looks at categories such as toxicity.
Another single-use plastic
Despite PLA’s environmental credentials, it has come under scrutiny. In a July report, nonprofit Beyond Plastics asserted that plastics — such as PLA — made from alternatives to petroleum are not necessarily better choices than petroleum-based options.
“The lack of regulations around bioplastics allows companies to present their products as more environmentally friendly than traditional plastic without meeting any standards for safety, toxicity, climate change impacts or how long it takes for them to degrade,” said President Judith Enck in a release at the time.
The Beyond Plastics report also took aim at the Biodegradable Products Institute, which works with brands to set and issue a compostability certification for packaging that is built on ASTM International’s compostable plastic testing standard. Beyond Plastics accused BPI of having built-in conflicts of interest because its board members are from some of the world’s largest petrochemical firms, including BASF and TotalEnergies Corbion.
BPI issued a response to the report and has pushed back on its conclusions. Executive Director Rhodes Yepsen said in an interview that BPI board members are required to operate in the best interest of the purpose of the organization — even in cases that would represent a conflict for their business operations. He gave BPI's prohibition of PFAS chemicals in any BPI-certified products — which goes beyond what the ASTM standard requires — as an example.
“We have a track record of showing that our membership and our board have been willing to support these bold moves,” he said, adding that working with industry representatives has been key to BPI’s ability to develop certifications that are both rigorous and widely accepted. BPI uses a third-party testing service, DIN Certco, to certify products against its specifications.
Enck, who declined an interview, said via email that “voluntary self-enforcing standards do not work” and that, in the case of BPI-certified products, she feels there is no way to mitigate BPI board members’ conflict of interest.
She called for federal standards around compostability and said that the FTC’s Green Guides, which do include language prohibiting false or misleading claims around compostability, are not adequate and have not been enforced. The Federal Trade Commission is currently reviewing its Green Guides for environmental marketing, with an update potentially coming this year.
Yepsen said he agrees that new materials should be scrutinized and that society needs to move away from disposable packaging.
“We're not advocating for a one-to-one replacement” from conventional plastics to compostable ones, he said. But he also believes that compostable biodegradable materials are “a really valuable solution.” And he thinks there is a risk that “poking holes in [compostable] solutions willy-nilly” will leave consumers with no choices aside from “incumbent” materials.
Performance, costs and life cycle
PLA’s sustainability profile is key to a brand’s sourcing decisions, but its performance attributes and costs are as significant, if not more, to buyers.
Relative to the more commonly used PET, PLA has low heat resistance and is a poorer gas and water vapor barrier, which limits its use in some food packaging applications. It is used in food service cups and clamshells, as well as straws and cutlery. PLA is still more expensive than conventional plastic.
Ford declined to provide Ingeo pricing. NatureWorks and TotalEnergies Corbion sell PLA resins with resistance to high heat, designed for applications such as single-use coffee pods. Ford said Ingeo grades made for high heat resistance are still designed to pass compostability testing. She also noted that British tea brand PG Tips has replaced its tea bags, previously made from compostable cellulose and polypropylene, with compostable PLA.
McDonald’s and Starbucks also use coated paper cups made with Ingeo PLA in areas of the country where ordinances requiring compostable food service ware are in place, she said.
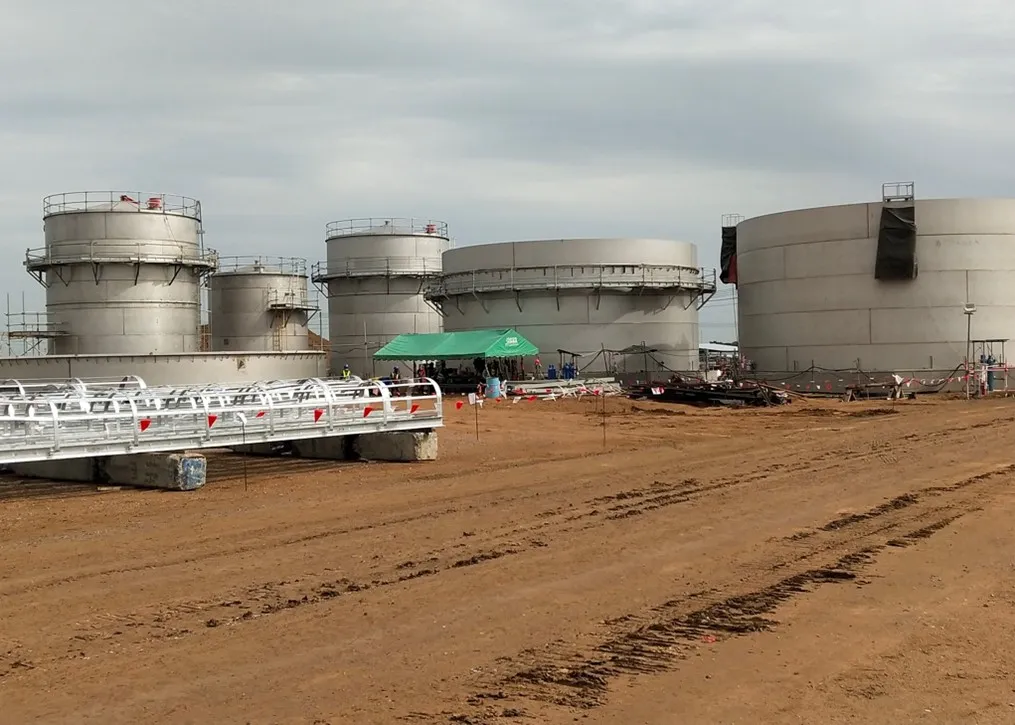
Performance and cost aside, it can be challenging to find data that clearly compares the environmental benefits of plant-based, compostable plastic like PLA to non-compostable plastic made from oil.
Studies show PLA production emits fewer greenhouse gas emissions than conventional plastics. TotalEnergies Corbion — citing from a European plastics trade group, internal sources and a PLA life-cycle analysis from one of its own scientists — claims its PLA has a 75% lower carbon footprint “compared to most traditional, fossil-based plastics.”
LCAs are an important tool, said Ramani Narayan, a Michigan State University professor and bioplastics expert whose work on PLA dates back to the 1990s when Cargill funded research in his lab. He feels they should always be performed to help ensure “there are no red flags in terms of [high] emissions … or the use of a chemical like PFAS.”
However, Narayan added, LCAs can be used to tell a specific story “based on where the boundaries are set” in terms of what inputs or outputs are or are not considered. LCAs have shown very different conclusions regarding the sustainability of corn-based ethanol.
Narayan said he often hears criticisms about PLA’s sustainability, since in the U.S. it is made from corn (in Asia it is sourced from sugarcane). He said producers such as Cargill generate many different products from corn, which has end markets including animal feed and corn starch for industrial products. In his opinion, this makes PLA demand an added value to farmers.
The sugar needed to source lactic acid can be derived from food waste, which would have the lowest environmental costs of any other source. But the systems needed to set up that supply chain are complex, and currently PLA is not sourced from waste materials at scale.
Another key factor when considering an LCA is whether it looks only at sourcing and production, known as cradle to gate, or also includes end-of-life factors, known as cradle to grave. Plus, not all LCAs consider the environmental impacts of agriculture, in terms of the land and water used to grow the crops. TotalEnergies Corbion’s LCA does include land-use changes, but it does not consider end-of-life factors. Academics say this is important because the PLA finished product stores carbon dioxide, and in an industrial compost environment that CO2 is released again as the PLA biodegrades.
Earlier this year, an NGO called the Plastic Pollution Coalition partnered with Eunomia Research & Consulting on a report focused solely on PLA, called “Bioplastics Are Trash.” It focuses on the climate effects of industrial agriculture systems that PLA manufacturers rely on to source lactic acid, and it says such agribusinesses can harm disadvantaged fenceline communities through air and water pollution. Public health impacts are also well-documented around petrochemical plants, too.
The compostability factor
Proponents say another key benefit of compostable food packaging, including products made from PLA, is that it can help divert any food left in the packaging into composting systems. The U.S. EPA estimates that emissions from food waste in the U.S. cause greenhouse gas emissions on par with 42 coal-fired power plants.
BPI certification tells the industry and stakeholders that the “packaging is compliant with industrial composting, that it's not going to pose a problem, that it will not persist and build up in the environment,” said Narayan.
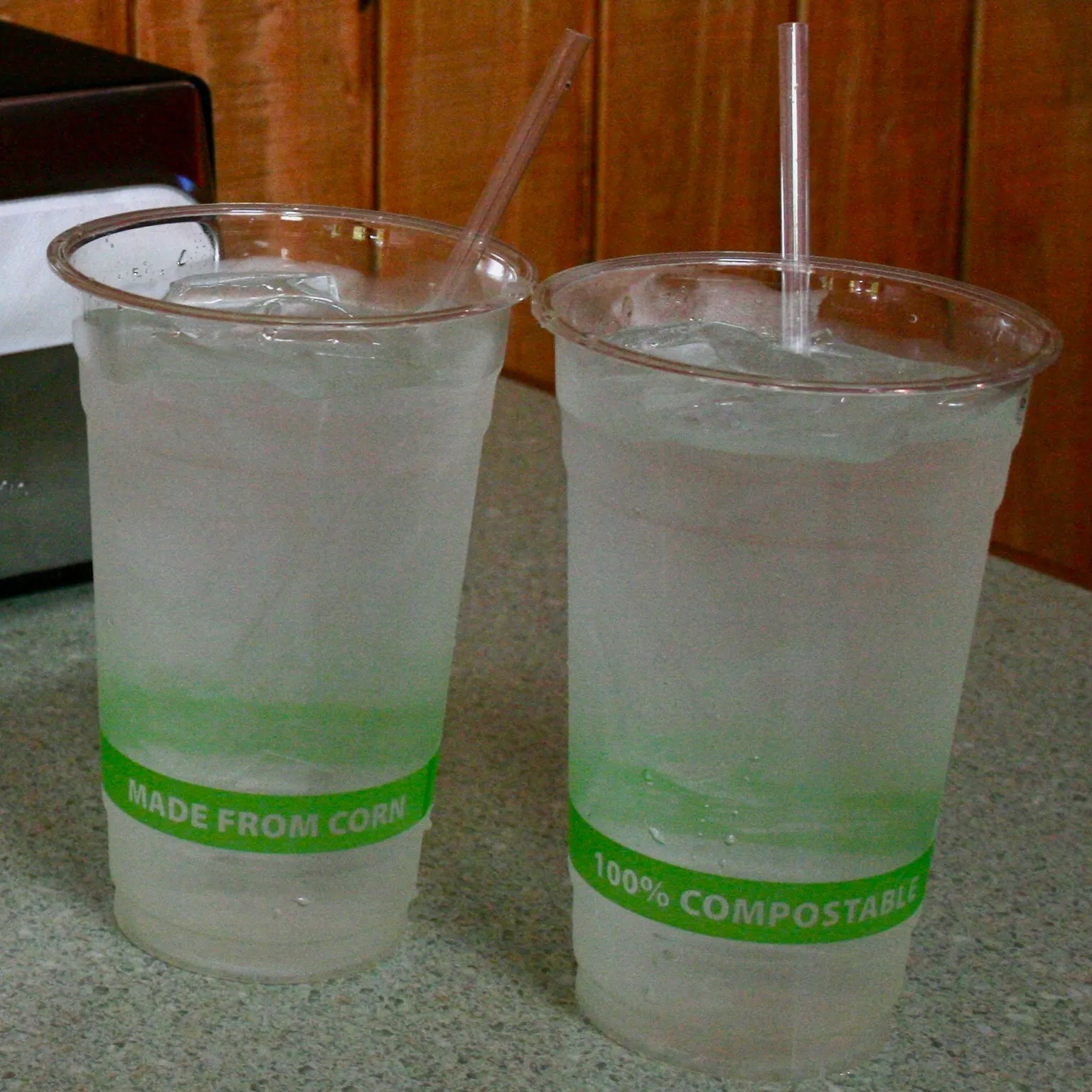
After finding that compostability in a lab setting does not always translate into compostability in real-world facilities, the Compost Manufacturing Alliance began offering its own testing services and publishes a list of proven compostable packaging materials, segmented by the type of industrial composting systems in which it will fully biodegrade. This list includes certain products made from PLA.
Other end-of-life options for PLA could include mechanical or chemical recycling, but market options are limited, and Packaging Dive was not able to find any major U.S. municipalities that currently suggest PLA should be recycled in their programs.
NatureWorks’ Ford confirmed this: “[PLA] Recycling isn’t happening more broadly in the U.S. mostly due to scale. There’s simply not enough PLA in the market yet to make it economical for recyclers to sort or collect PLA,” she wrote in an email.
This means that if consumers don’t have the option to send the material to an industrial composting facility, then it’s likely going to a landfill or incineraor. And that bothers Neil Edgar, the executive director of the California Compost Coalition and a board member of the U.S. Composting Council.
“The idea is that if PLA is fully composted, then it's not going to be a problem,” he said. “But that's a big ‘if.’” Edgar estimates that of all the PLA packaging in use today, exceptionally little of it actually gets composted.
The Plastic Pollution Coalition’s report notes that the lack of composting infrastructure, and the fact that PLA can biodegrade in landfills or when littered, makes this a concern. It concluded that without “appropriate policies and regulations to minimize or eliminate unintended and negative production consequences,” PLA is not necessarily a sustainable choice.
According to BioCycle’s 2023 survey of residential composting systems, only about 12% of U.S. households had access to municipally-supported curbside or drop-off food waste collection systems. Such composting systems are growing, thanks to policies that require states to develop organics recycling infrastructure, but problems with conventional plastics contamination has led some composters to stop accepting compostable packaging.
Plus, U.S. Department of Agriculture rules say nothing that is put into compost can be synthetic if composters want to certify their product as organics, meaning they cannot accept PLA. Last year, BPI submitted a rulemaking petition requesting that the agency revise its regulations on allowed compost feedstock to include materials that meet ASTM International’s compostability standards. The agency is set to consider the petition at a meeting in late October. If it does not change the standard, composters who sell their product under the organic legislation will need to continue filtering out PLA and other compostable packaging material.
PLA that ends up in landfills — whether because industrial composting isn’t available or because it is filtered out at the pre-processing stage — will fragment and likely decompose over time, releasing a greenhouse gas more potent than carbon dioxide.
“Under those [anaerobic] conditions, the biological environment converts this to methane,” said Narayan. Methane is 25 times more potent than carbon dioxide over a 100-year period. NatureWorks commissioned a 2011 study that found the amount of methane PLA releases depends on many variables, including geography and landfill management practices.
As for the litter factor, some amount is conisdered inevitable even in areas with good waste collection infrastructure.
A meta-analysis study published this summer, and sponsored by bioplastics manufacturers, indicated that PLA will eventually biograde as it fragments into increasingly smaller pieces in the presence of some moisture or water. However, Edgar questioned the study’s utility since it did not conclude whether PLA fully biodegrades in terrestrial environments, nor did it show the time or temperatures needed for PLA to fully biodegrade in water.
The NGO 5 Gyres, which advocates for reducing single-use plastic and preventing plastic pollution, put plastics through biodegradation tests in the real world. The results, which includeed PLA products, were highly variable based on polymer type and form factor.
Evolving policies are changing the stakes
Along with growing demand for PLA, there’s an expanding list of state and federal policies that will impact the PLA market.
In addition to the USDA’s consideration of compostable bioplastics, pending policies or reports across a handful of other federal agencies could emerge before the end of President Biden’s term and potentially affect material choices in packaging.
Beyond that, five states are beginning to enact extended producer responsibility laws that are impacting brands’ packaging choices. But Ford said that until states sort out specific requirements and costs in their EPR laws related to the use and handling of compostable packaging, some brands remain in limbo about what this will mean for compostable packaging.
“If you go to Whole Foods and you buy Off the Eaten Path — that's one of Pepsi's products that's made with Ingeo — [it comes in] a beautiful compostable package. Why aren't all the chip bags compostable yet? It's because of very real concerns about what is EPR going to cost. Where does compostability fit into EPR? What requirements are there going to be around safety of materials? That's a very hot topic right now,” Ford said.
Edgar said it’s imperative that the proper composting infrastructure and incentives grow in lockstep with the PLA market, because PLA “is not a panacea” to the problems associated with plastic waste. If PLA ends up in landfills or, worse, the environment, he said, “it's another take-make-waste product — another single-use plastic.”
Interested in more packaging news? Sign up for Packaging Dive’s newsletter today.