At a recycling industry conference last year in Florida, Chang Dou saw something that made him realize the importance of his research.
“The conference provides all PLA containers ... But there's only one recycling bin,” said Dou, a senior scientific engineering associate at the Advanced Biofuels and Bioproducts Process Development Unit at Lawrence Berkeley National Laboratory, during a visit to his lab in Emeryville, California. He saw no bins for compostable plastics. “And I saw everyone throw [their PLA container] into the recycle bin.” Given that it was an industry conference, he assumed many of the attendees did this, “knowing they won't be recycled at all.”
By then, he and his colleagues had already completed proof-of-concept research to demonstrate a process for breaking down a mixture of conventional and bio-based plastics using a biological process. The work received funding from X, a division of Google that describes itself as “the Moonshot Factory.” X declined to specify the exact funding level. The commingled polylactic acid and polyethylene terephthalate he saw in those bins could be feedstock for the process the team has developed.
Their motivation was to create a process for recycling mixed plastics that both avoids the high energy and emissions used in certain currently-available processes, such as pyrolysis, while also creating a means for producing valuable and biodegradable polymers.
Late last year, Dou and his colleagues published a paper in the journal One Earth that details the approach. In a streamlined “one-pot” process, a 1:1 mixture of PET and PLA is chemically depolymerized down to their monomers. These monomers are then bacterially fermented into a type of bio-derived polyester called polyhydroxyalkanoate, which can be used in certain packaging applications.
The first step requires just water, heat and an ionic liquid as inputs. By avoiding high heat and the use of chemical reagents or metal-based catalysts to separate the materials, the researchers do not need to do any additional processing before adding microbes for the PHA conversion.
The researchers consider the results promising. Roughly 95% of the mixed PLA/PET plastics were degraded into their monomers, and then these were microbally converted to PHA. What’s more, they say this approach to manufacturing PHA could lower production costs by 62% and greenhouse gas emissions by 29%.
While this research project did not use polyester textile feedstocks, the team has also submitted a concept paper to the U.S. Department of Energy to explore commercializing the first step — depolymerization — for textile recycling.
Dou’s colleagues Ning Sun, ABPDU research scientist, and Hemant Choudhary, deputy director of catalytic lignin depolymerization at the Joint BioEnergy Institute (a DOE research project) and a scientist at Sandia National Laboratories, co-led the research along with representatives from X. This follows multiple years of research and investments by Google into plastic recycling issues.
The team decided to use PET and PLA for the experiment based on a number of factors. Both polymers are polyesters, which the team said is a relatively easy starting point for testing this microbial process. PET’s abundance in the marketplace was another driver. The researchers also note that PLA packaging is a growing market, yet the proper handling of PLA is made difficult by the fact that it often looks so much like PET.
Because MRFs generally do not accept PLA for recycling, organics recycling is the main option. But that, too, is a limited option. Dou, pointing to a map of industrial composting facilities in the United States, said the lack of composting infrastructure outside large metropolitan areas is another reason that new ideas are needed for recycling PLA.
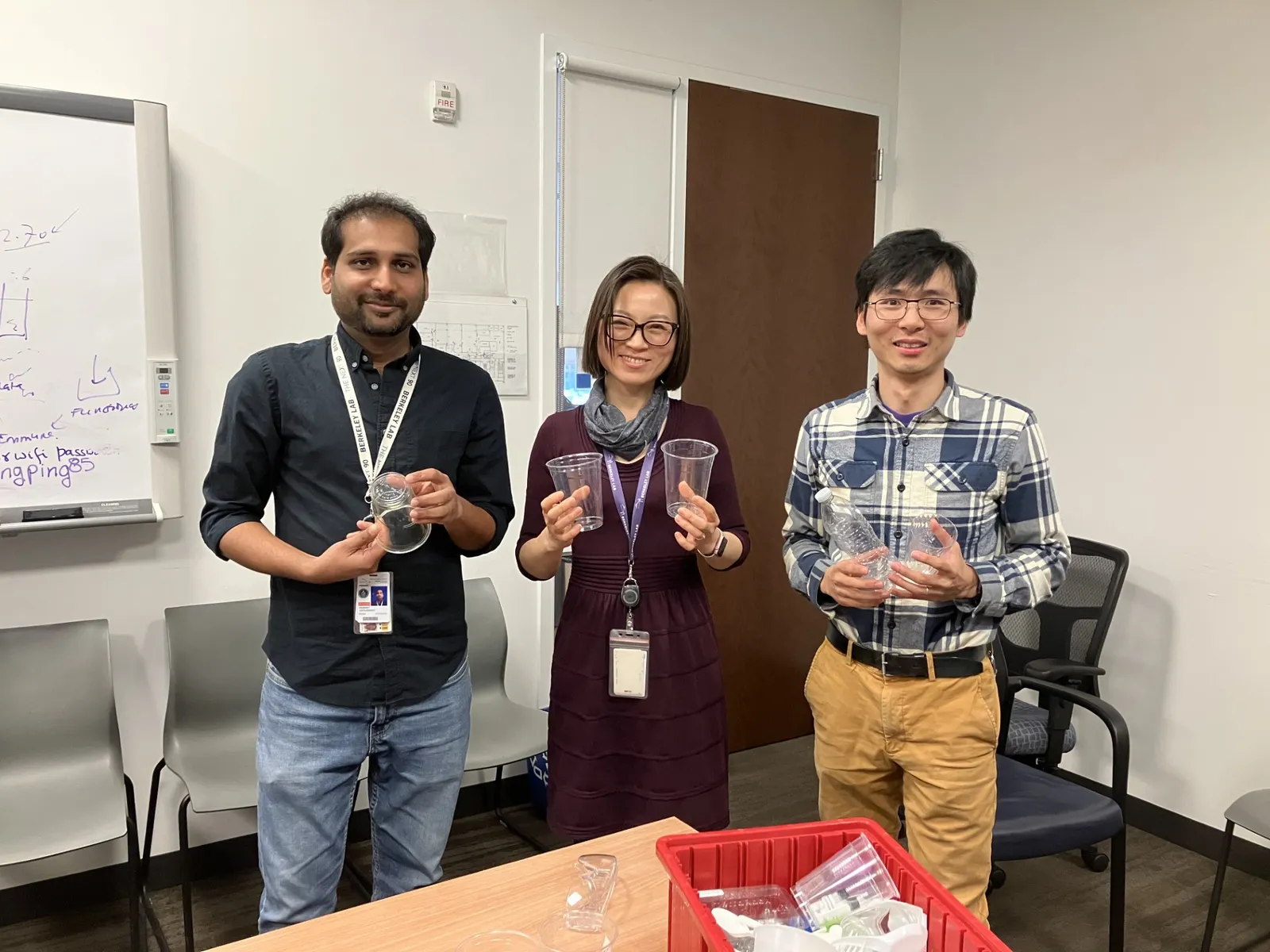
Bioplastics innovation landscape
The Biden Administration has called for more bio-based and “recyclable-by-design” plastics, and the topic is seeing increased attention.
A 2022 report from the Government Accounting Office said advances in biological recycling, based on the use of enzymes, showed promise. Researchers from the National Renewable Energy Laboratory have found that enzymatic pathways for recycling PET could be scaled to derive terephthalic acid at cost parity to petroleum-derived terephthalic acid. And French startup Carbios has engineered an enzymatic approach to depolymerizing PET into its monomers and then making PET from those. It has a pilot plant and expects to open its commercial plant next year.
Rather than employing enzymes to break down the plastic, Dou and his colleagues use ionic liquids as catalysts, specifically ones that are biocompatible and not metal-based.
Dou said that selection was important for two reasons. One: using biocompatible ionic liquids allowed them to add a microbe to the same reactor used for depolymerization without having to do any processing or separations, because metal-based catalysts can be toxic to the microbes. Second, the sourcing of catalysts containing copper or iron presents red flags, said Choudhary, because “we are already having metal scarcity all around the world.”
Hal Alper, a professor in the McKetta Department of Chemical Engineering at the University of Texas at Austin, said the ability to chemically recycle a mix of polymers is notable, calling it “an alternative to the pyrolysis processes that can deal with mixed wastes and also provides for the raw monomer generation.”
Alper agreed that avoiding metal catalysts is important for ionic liquids. But he noted that enzymatic recycling, like the PETase enzyme that Carbios uses, does not contain metals.
This isn’t the first time chemical and biological pathways have been successfully used to recycle mixed plastics.
In 2022, researchers with NREL’s BOTTLE research project used metal-based ionic catalysts to break down a mixture of polyesters and other plastics. After removing the metals, the material was then converted, using two strains of the same microbe Dou and his team would later use in the PET/PLA work. According to Chemical and Engineering News, one strain can be used in biodegradable packaging while the other can be used to make nylon-like materials that could be recycled.
Choudhary said the biggest benefit of the Berkeley team’s one-pot approach could be its energy efficiency. He said the multi-step processes that burn heat energy and release carbon dioxide can erase much of the benefits of chemical recycling and also drive up costs.
The scale of energy intensity varies, with pyrolysis being a high-energy process. But any process that requires separation, even the process that NREL developed with metal catalysts, would use more energy than the type of one-pot approach the Berkeley team has developed. But Choudhary noted that a key advantage to NREL’s process is the ability to recycle polyolefins and polyesters together.
“We believe it is important to develop multiple solutions (ours, NREL's, and many others) and analyze them at pilot or relevant scales based on [techno-economic analysis] and [lifecycle analysis] to have a better understanding or be able to actually compare these processes,” Choudhary wrote in an email.
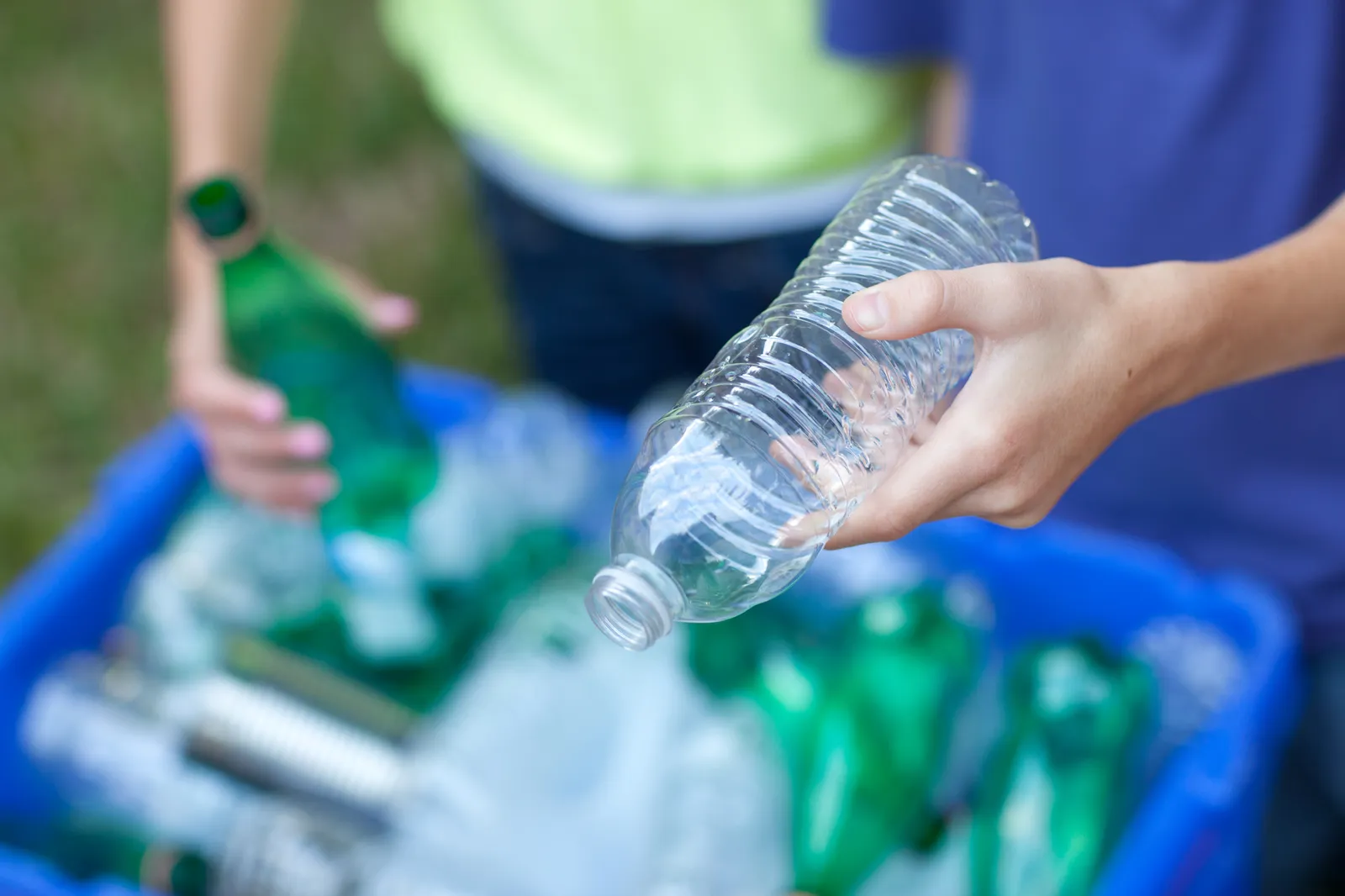
Market applications
John Standish, technical consultant and PET technical committee lead with the Association of Plastic Recyclers, said he’s been encouraged by research coming out of academia and national laboratories. In particular, he praised NREL’s BOTTLE project, which has forged industry partnerships with companies such as Amazon, KraftHeinz, and Procter & Gamble.
At the same time, Standish said PLA’s current packaging market penetration is “negligible.” Regarding PLA contamination in the PET recycling, he said, “if it is a problem, it's not one that shows up on the radar screen because there's several others that are bigger.” He suspects infrared sensors would divert any PLA out of mechanical PET recycling streams and into the waste stream.
In terms of collecting polyesters for any future commercial applications, the Berkley researchers acknowledged that mechanical PET recycling is well established and would be difficult to compete with in the near term. That would mean collecting polyester or other form-factors that would not be part of PET streams for mechanical recycling.
However, Sun said their research paper’s techno-economic and lifecycle modeling assumed specific PLA and PET sorting at a MRF. Another option would be to target MRF residue, which contains different types of plastics, but only convert polyesters using their process.
Dou noted that well over half of the PET used in North America does not get recycled. (The latest data from NAPCOR is that the U.S. PET recycling rate in 2022 was 29%, while the North American rate was 37.8%.) That means the majority is still going to landfills or incinerators.
The core technology the team is developing is designed for any polyester. The team said they used PLA because it’s a growing market, in part due to demand for compostable packaging. Alper concurred that PLA use is growing, indicating that contamination in PET streams “would be an issue for the future.”
While PLA accounted for the smallest plastic feedstock going into MSW as of the U.S. EPA’s 2018 data, some research indicates that developing markets are leading the push for more PLA, which one research report said could scale by a compound annual growth rate of 21.4% from 2024 to 2030.
Standish said that if Dou’s team could use its chemical recycling and biological upcycling approach to recycle PET fiber for textiles, which most polyester production goes toward, that could be a game changer. “The time for textiles is today. We need this today,” he said.
Dou and his colleagues stressed that their research is focused on the entire esters group, and therefore could be applied to polyester textiles — although to date it has only been proven on a 1:1 mixture of PLA and PET plastic cups.
Another important open question is how disposal-bound mixed polyesters, in all form factors, would be intercepted and collected for this chemical recycling process. The researchers said one option would be to source this material from MRF residue streams, where non-bottle PET is still common.
Still, the researchers said the efficiencies gained from both depolymerizing and then converting the monomers into a new polymer in one vessel is an important advance. In fact, Sun has been focused on this for many years.
“We definitely want to continue,” she said. Now that the lab’s collaboration with X is completed they’ll need new funding to move the work forward, starting with scaling up to large batches in the ABPDU lab.
“We’ve only done an initial demonstration,” said Sun. “This process is promising, but if we want to really bring this into the market, there's still a long way to go.”
Correction: A previous version of this story had incorrect information about the level of funding X provided.