When Rumpke Waste & Recycling set out to design its latest recycling center, the company planned to have the latest technology meant to pick out extremely specific items — partly in response to rising demand for “hard-to-recycle” materials.
Rumpke expects that more chemical recycling companies will express interest in buying those hard-to-recycle materials once their plants come online in the next few years.
Under its current operations across its multiple MRFs, Rumpke is not yet baling and selling any material to chemical recyclers, but it recently signed an agreement to send bales of colored PET to Eastman’s planned facility in Kingsport, Tennessee, in the coming months.
Eastman says it plans to turn the material it receives from Rumpke into “virgin quality polyesters” to be used in packaging applications. Rumpke’s 200,000-square-foot facility in Columbus, Ohio, is expected to have 19 optical sorters and other artificial intelligence-assisted technology that could help with the process.
Some chemical recyclers have already announced agreements with major brands to use chemically-recycled plastic in everything from reusable water bottles to food packaging, and some of those items are already available on store shelves in limited applications.
At the same time, chemical recyclers are continuing to ink deals with MRF operators, private companies and specialty collection partnerships to source enough material to fulfill their production promises.
Such partnerships could soon represent a turning point for how MRFs and other collectors process, market and sell plastics that are currently considered waste or have very limited markets, said Jeff Snyder, Rumpke’s director of recycling.
Large companies like WM also see the potential to plug into chemical recycling markets. Tara Hemmer, WM’s chief sustainability officer, said in a November interview that the company is open to building strategic partnerships to manage hard-to-recycle plastic. “In the future, there will be a place for chemical recycling” in WM’s materials management strategy, she said.
However, the future trajectory of the chemical recycling market will influence how companies make those business decisions, Snyder said.
“Like with anything, you have to have an end market for the material,” he said. “I'm open to it in the future, as long as it makes sense from a price standpoint, a market standpoint. I think chemical recycling is the future for some of those hard-to-recycle plastics. But we’re still all about mechanical recycling first.”
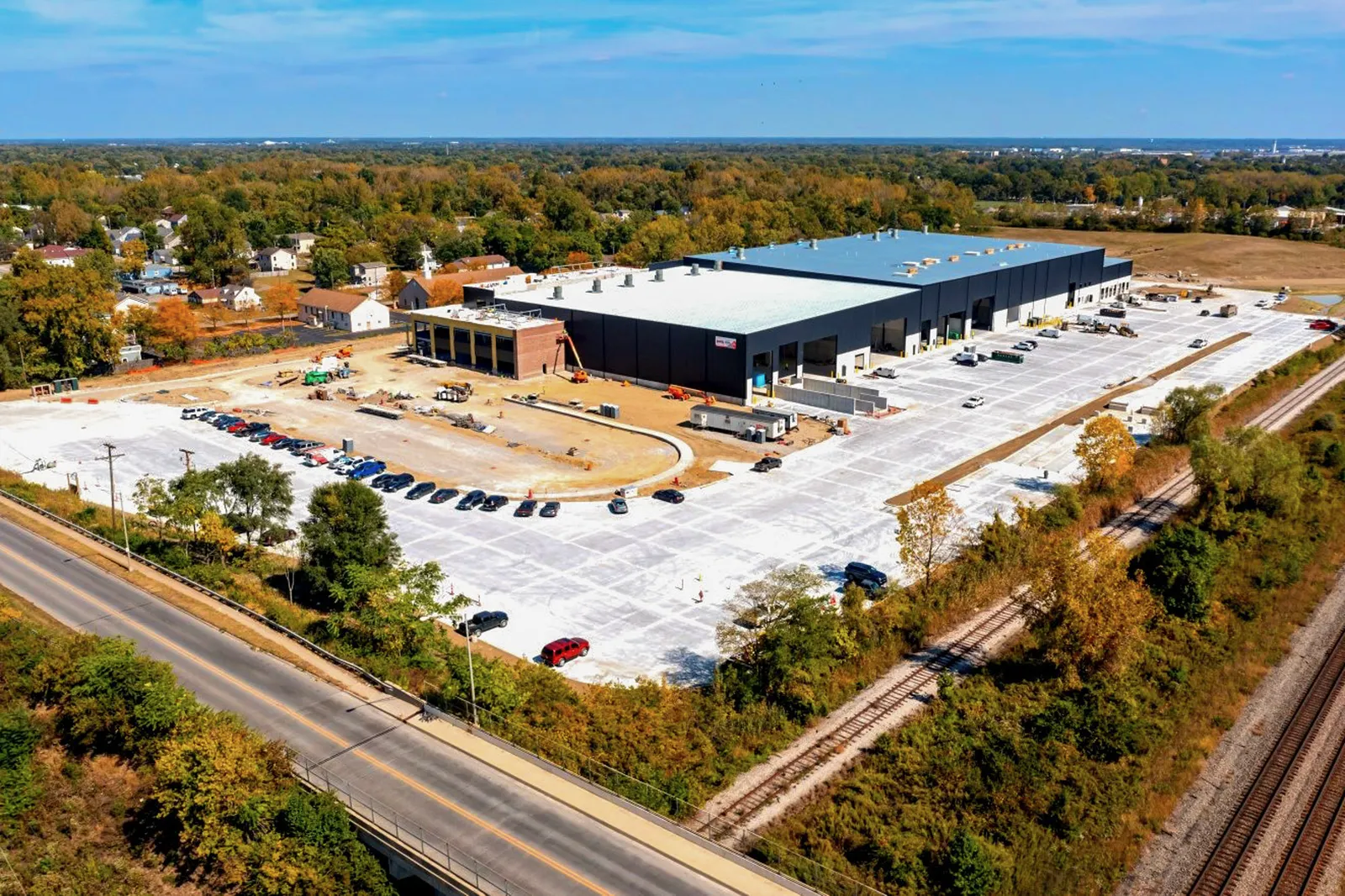
Measuring the market
Chemical recycling, also described by the plastics industry as advanced or molecular recycling, is a broad term for numerous processing technologies that break down recovered plastics to the molecular level to become “building blocks” for new plastics or other products. Common techniques include pyrolysis, gasification and depolymerization.
Companies such as Dow, Eastman, LyondellBasell, ExxonMobil, PureCycle, Cyclyx and others are investing millions of dollars a year in an effort to scale these technologies, saying the investments will divert hard-to-recycle plastics from landfills and transform them into new products.
There are about 11 chemical recycling facilities up and running in the U.S., according to data collected from Beyond Plastics, an advocacy group that is against chemical recycling. Global Partners For Plastics Circularity, a group of plastic industry associations that support chemical recycling technologies, estimates five companies additional projects under construction in the U.S. More are in the works: Last month, for example, Eastman announced plans to build a second facility in Longview, Texas, following the announcement of up to $375 million in funding from the U.S. Department of Energy.
Such companies tout these announcements as a sign that chemical recycling is already making a dent in the recycling world, but it can be hard to know just how much chemically-recycled feedstock is being produced right now and how much of those feedstocks are ending up in new products.
That’s partly because some chemical recycling companies are still in the process of building out production plants, while others have announced offtake agreements but have not yet started purchasing the feedstock or delivering resin.
The chemical recycling industry could provide major revenue opportunities in coming years, but only if companies can jump hurdles such as “high initial investment costs, technological constraints, and the need for supportive legislative frameworks,” according to a market assessment from Fairfield Market Research. If such conditions are met, chemical recycling projects in North America could grow faster than anywhere else in the world.
By 2030, total market revenue from chemical recycling companies around the world could be as high as $50 billion, rising at a compound annual growth rate of 30% between 2023 and 2030, the research report said.
Chemical recyclers say they are a growing part of the value chain because they’re in a unique position to find uses for material that normally has few reliable end markets. However, it could be a while before that market potential translates into an established, long-term market for lower-value plastics, Snyder said.
Snyder said other chemical recyclers have expressed interest in buying material from him, but in the case of one company that requested test bales of material, those bales “are likely still sitting in their warehouse, because they’re not up and running yet, and we’re not sure when they’ll be,” he said.
Sandeep Bangaru, vice president of circular economy platforms at Eastman, said his company and others can have a hand in creating a “stable, solid end market” for previously unwanted plastics. Such plastics still have market value, despite experiencing similar price volatility to more established plastic grades.
“We're taking this material, but we're not getting it for free. We're buying this material, and we're getting it back into high-quality packaging,” he said. “We’re demonstrating that the economics are workable to do this and we want to scale that much more broadly.”
Though analysts expect chemical recycling to become more of a presence in coming years, the industry is still too new to forecast how future recycled plastic demand from such companies could impact the market. That’s because many facilities that are actively searching for material are still scaling up or in early stages of operations, while some other planned facilities are facing delays, said Andrea Bassetti, senior analyst for plastic recycling at ICIS, during a presentation at the Plastics Recycling Conference in March. In coming years, chemical recycling “isn’t really a market disruptor, more of a market enhancer,” she said.
Proponents say major companies have invested millions over the years and are now in a position to scale their technologies and move forward with executing on offtake agreements, some of which were inked several years prior. Major companies such as Dow count advanced recycling efforts toward broader ESG goals, while Eastman said its chemical recycling technologies will help achieve its U.S. Plastic Pact goal to ”effectively recycle or compost 50% of plastic packaging by 2025.”
But critics say chemical recycling companies won’t be able to manage the volumes of material they claim and are misleading customers by characterizing their work as a sustainable way to keep hard-to-recycle plastics from disposal. They note that numerous companies have experienced delays in opening their facilities or other setbacks.
Critics of chemical recycling, including Beyond Plastics, pointed to the recently announced closure of Regenyx in Oregon as one example of what they said was a high-profile failure of a chemical recycling company to turn a profit. Regenyx, a polystyrene chemical recycling joint venture between Agilyx and Amsty, plans to close by April 30.
The companies characterized the closure as the result of “successfully achieving the objectives defined in its five-year formation agreement,” but according to Sustainable Plastics, the facility reported losses of more than $4.58 million between 2021 and midyear 2023. Regenyx was expected to process up to 3,650 tons of PS a year, but had reported processing closer to 4,400 tons between 2019 and 2021, according to the report. Sales were also lower than expected, according to the publication.
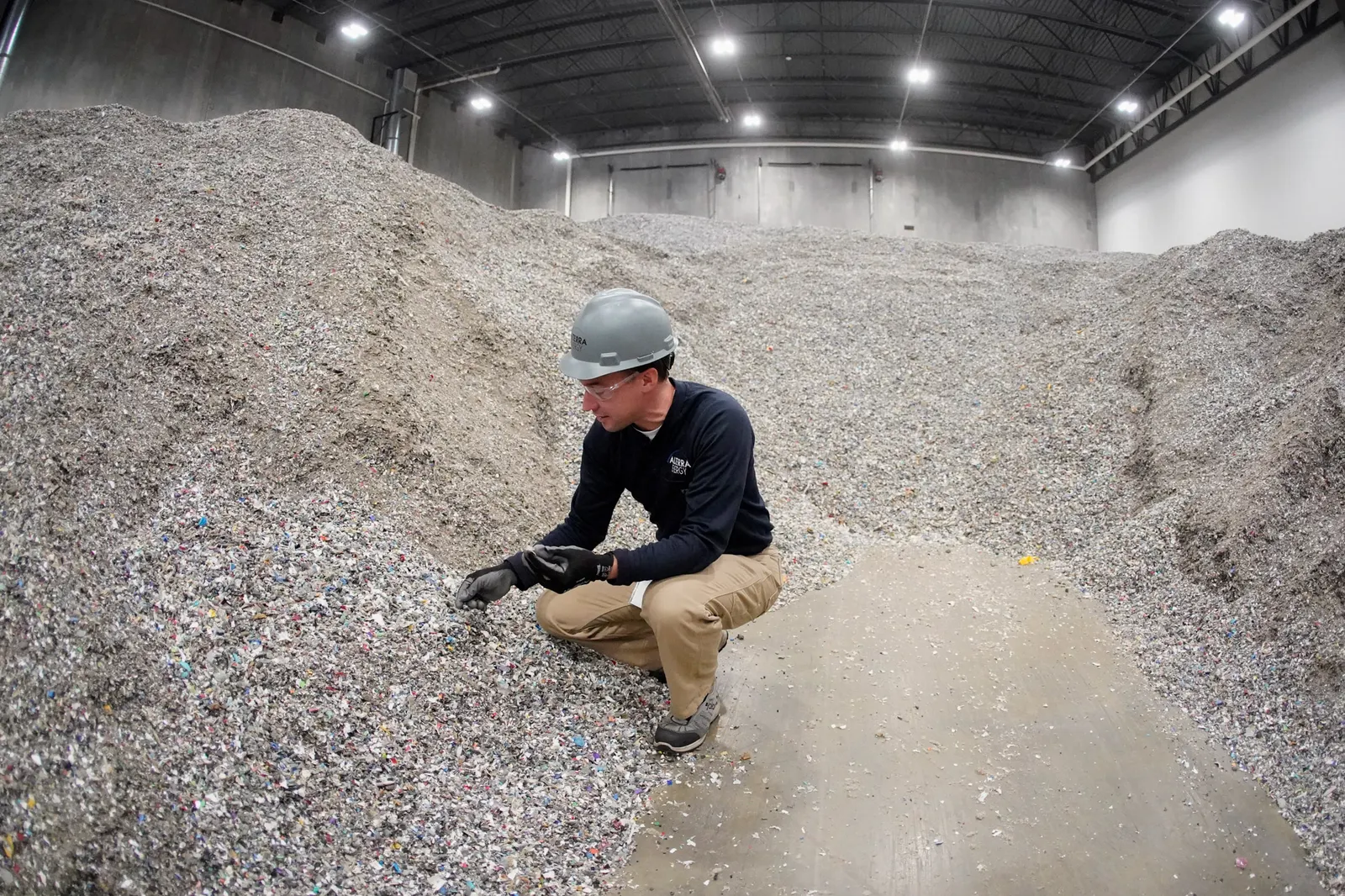
Collection strategies
To weather the changing economic and business environment, chemical recyclers will still need to rely on a range of strategies to collect the materials they need to be successful, said Jeremy DeBenedictis, president of chemical recycler Alterra Energy.
DeBenedictis, whose company is based in Ohio, said relationships with MRFs are a big part of how Alterra gets the material it needs to create a pyrolysis oil it sells to manufacturers for plastics-to-plastics applications.
Between 60% and 80% of the plastic the company processes is “postconsumer residue material” coming from secondary sortation facilities and MRFs. The company mainly wants polyolefins and steers clear of more commonly-recycled plastics like PET. “We get some stuff that comes to us after it's been sorted from curbside collection,” he said, as well as plastic from post-industrial applications.
DeBenedictis said in a November interview that he often brings material from his own house to use as feedstock, too, including “the flexibles like the chip bags, the granola wrappers, the candy wrappers from Halloween.”
Alterra has an overall capacity of about 20,000 tons per year. It currently ships its pyrolysis oil to up to six customers based in the U.S. Gulf Coast region and Europe. DeBenedictis declined to describe the customers, but said the company plans to publicly announce certain partnerships sometime in 2024.
Alterra is open to partnering with other MRFs and secondary processors for more plastic material and sees this as a way to help facilities find homes for prohibited materials that may already be in the material stream, like plastic bags and bulky rigids.
Another chemical recycler that aims to source postconsumer plastic feedstock from MRFs is 245Recycle, which announced in February that it would “build, own and operate” a 400-ton-per-day pyrolysis facility in an unspecified area of Texas’s Gulf Coast. The facility, set to be operational by 2027, will source postconsumer plastics for its pyrolysis process, it said.
Another work in progress is a chemical recycling plant in Statesboro, Georgia, run by German company Revalyu Resources. The company plans to recycle 200 million pounds of postconsumer PET per year when it’s operational by 2025. Revalyu is investing more than $200 million in the glycolysis facility, its first U.S. location, which it expects to be similar to one already running in India. The company broke ground on the facility in October.
Though MRFs could have a major role to play in collecting and selling the plastic that chemical recyclers want, the plastic is also coming from other sources such as dropoff programs, commercial and post-industrial collections, and specialty partnerships. Some pilot programs are also collecting such material from curbside programs, though critics say that process can create more contamination for more readily-recyclable items already in the bin.
Cyclyx International, a joint venture among Agilyx, ExxonMobil and LyondellBasell, announced in December that it would build a facility in Houston with the capacity to produce 300 million pounds of plastic feedstock per year using proprietary technology that involves both chemical and mechanical recycling methods. The companies originally slated the facility to open in 2024, but it is now expected to open in mid-2025.
The company says its facility, called the Cyclyx Circularity Center, will source a variety of postconsumer, commercial and industrial plastic scrap, “including difficult-to-recycle materials, such as food packaging, chip bags and bottle caps.” ExxonMobil and LyondellBasell are investing $135 million into the project and will have offtake rights from the facility.
Meanwhile, Eastman has been lining up several partnerships for feedstock in advance of its Kingsport location opening. That facility, which Eastman bills as the “world's largest material-to-material molecular recycling facility,” expects to recycle a total of 110,000 metric tons of “hard-to-recycle plastic” each year from numerous sources.
It plans to partner with Food City, a southern grocery chain, to set up customer drop-off sites for plastic packaging such as “water bottles, colored laundry and shampoo bottles, trays and fruit containers among many other plastic items.” Those drop-off sites, including three in Kingsport, are expected to roll out in the coming weeks. Eastman said the material it collects will be processed at Kingsport for durable good applications, as well as packaging and textiles.
Bangaru said the company finds the majority of the feedstock it needs for its Kingsport facility within 500 miles, with more prospects in the works. Eastman says MRFs and reclaimers are ideal candidates because it’s a win-win partnership, but other types of collection points serve to complement that partnership.
“This stuff shows up in their No. 1 bale where they only want to clear bottles. This is yield loss for them,” he said. “So we thought, could we get this material even upstream of them?”
Grocery store collection is also a strategy for Ahold Delhaize’s subsidiary Food Lion. Last year, numerous Food Lion locations served as collection points for plastic packaging as part of a pilot project to make food-contact overwrap from chemically recycled plastic. After collection, Cyclyx sorted and pre-processed the packaging materials before delivering them to ExxonMobil's Baytown, Texas, chemical recycling facility.
Just as companies are looking to build more partnerships to source feedstock, DeBenedictis said he feels there’s a need for more chemical recycling plants in order to make the level of impact needed to divert millions of plastic that are otherwise landfilled each year. The U.S. EPA says 27 million tons of plastic were landfilled in 2018, the most recent year for which the data is available.
“Right now, I don’t see the others as competition. We’re rooting for all of them — the Eastmans, the Agylyxes, the Exxons,” he said. “We’re going to need them all if we really want to make this work.”
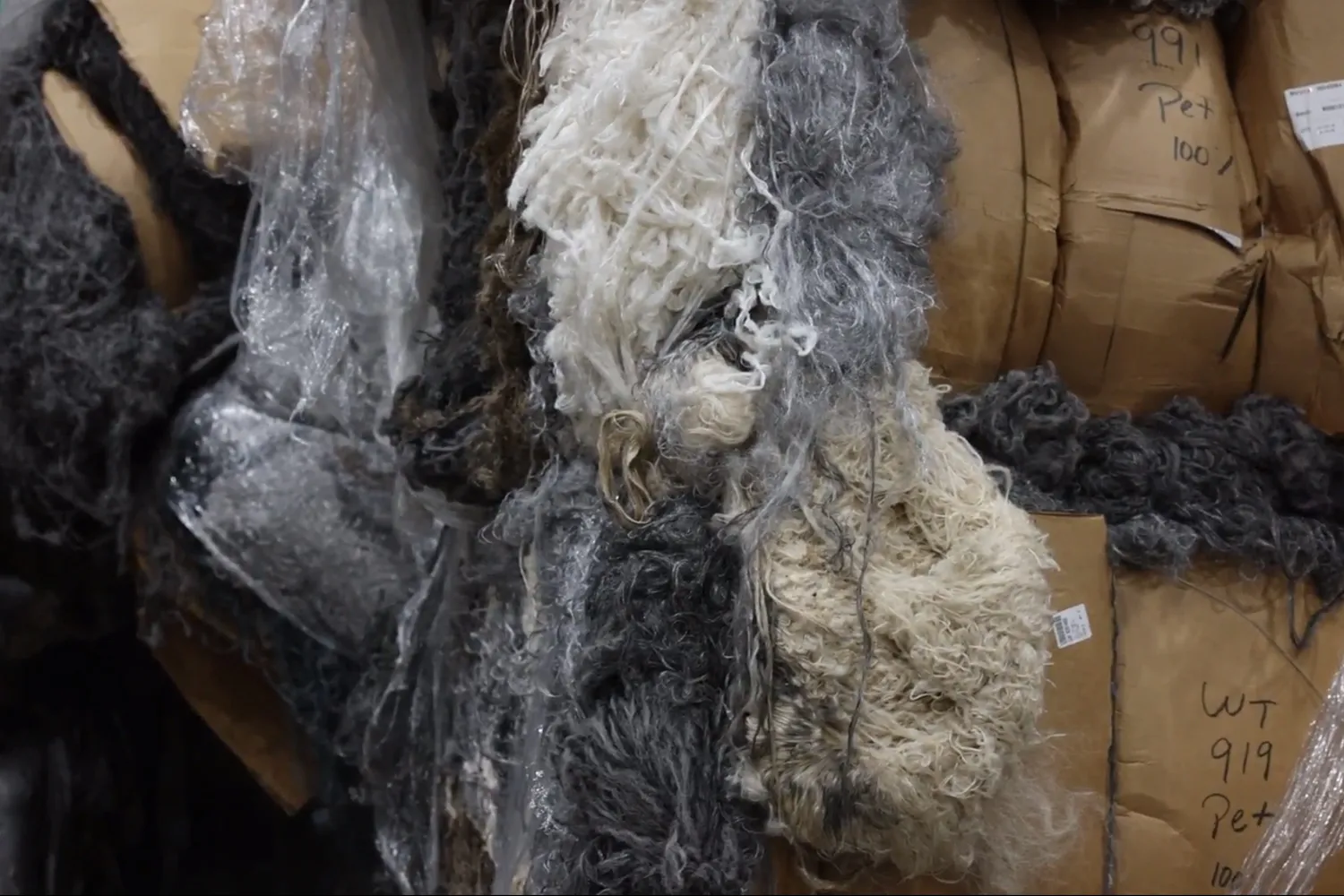

Facility productivity hurdles
While DeBenedictis anticipates a more crowded chemical recycling market in the future, many of the major chemical recycling facilities that have been announced are still in the process of being built or scaled up. At the same time, several facilities have faced issues with opening or scaling on the timelines they originally proposed.
Opponents point to repeated setbacks and a lack of information about the delays as one of the troubling aspects of chemical recycling’s marketing, saying the facilities’ promised outputs don’t match their performance.
Beyond Plastics, which criticized the chemical recycling industry in a detailed report last fall, said such delays have been happening for years. The nonprofit said the industry has yet to prove it can make good on its promise to be a reliable plastic waste solution. “This is a common storyline with chemical recycling: delays, barriers, cost overruns, and pollution,” the report said.
Meanwhile, the American Chemistry Council said such recycling technologies are “rapidly growing” and continued investments are necessary to advance what it calls “plastics circularity.”
One facility experiencing repeated setbacks is PureCycle, a company that does not consider itself a chemical recycling company but uses a solvent process to break down PE plastic in a similar way to some other companies under the chemical recycling umbrella.
PureCycle paused production for more than a month when its Ironton, Ohio, plant experienced a significant power outage in August. The company now faces a class action lawsuit from investors who said they were not informed of the outage until months later and were misled about PureCycle’s productivity during that time. The case is still moving through the court system, with a federal judge recently setting deadlines for when Purecycle would need to file a motion to dismiss and when the plaintiffs would need to file revised complaints.
In a December interview, CEO Dustin Olson said he wasn’t “at liberty to speak about the lawsuit” other than to say “we're working through the processes and we're collaborating with the different groups to get to resolution.” Olson said such setbacks “happen across the normal course of business,” and that the plant was back up and running.
At full capacity, PureCycle expects its Ironton facility to produce about 107 million pounds of PP resin each year. He touted PureCycle’s recent shipment of recycled PE to Milliken as a milestone, and said it also lists Procter & Gamble and L’Oreal as “big customers.”
PureCycle receives its PE feedstock from several places, including iSustain, a plastic recycler “solutions provider” that signed an agreement earlier in 2023 to provide up to 10 million pounds of postconsumer polypropylene. iSustain, which also provides feedstock to chemical recycler Nexus Circular, recently announced on its website that it was looking to collect more kinds of PE plastic — such as LDPE mattress bags and gaylord box liners — as feedstock to deliver to its clients.
Repeated facility delays have led to high-profile chemical recycling projects being scrapped before completion. Brightmark Energy and the Macon-Bibb County Industrial Authority ended an agreement in 2022 to build a $680 million chemical recycling facility in Georgia. Brightmark missed a deadline to deliver “end products” to customers of one of its locations in Indiana, which was a condition of its contract with the authority.
Brightmark’s Ashley, Indiana, facility is still in the startup phase.
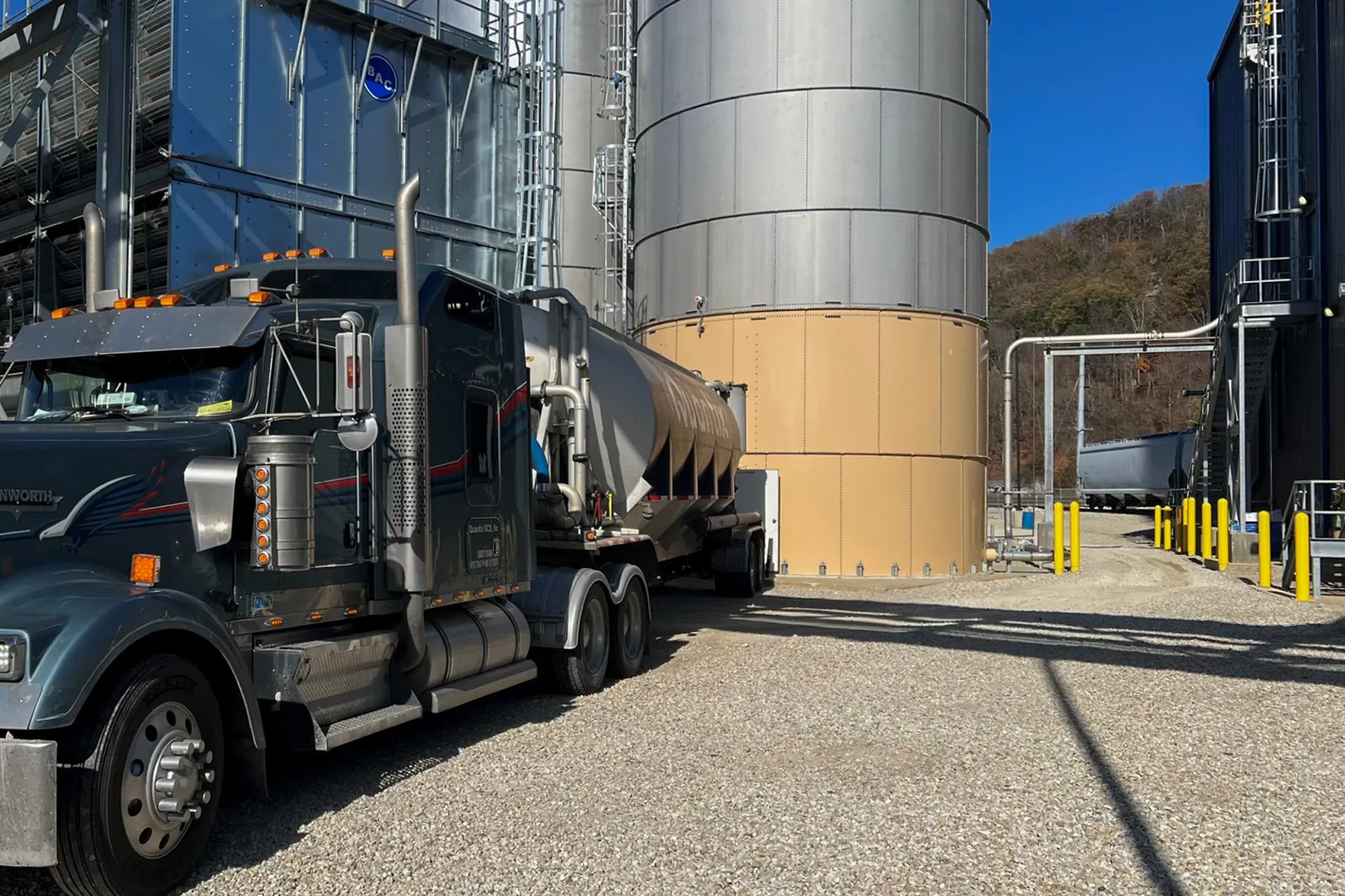
Product announcements
Though some productivity hurdles remain, several notable packaging and durable goods companies have already announced that they’re integrating chemically recycled feedstock into their products.
Companies like Berry Global and Printpack say some of their plastic food packaging, such as single-serving fruit or bean cups, contains a percentage of chemically recycled feedstock. Berry has signed agreements to use chemically recycled feedstock from U.K.-based Plastic Energy, while some of PrintPack’s packaging uses feedstock from ExxonMobil’s proprietary Exxtend technology. SEE (formerly known as Sealed Air) and Ahold Delhaize last year announced they would also use Exxtend technology to make certain food-contact plastic packaging.
Amcor says it has incorporated chemically recycled content into numerous kinds of packaging, including for condiments, diaper overwraps and shrink film for bottled water. In 2023, some of that chemically recycled plastic came from “certified circular” PE and PP from ExxonMobil’s facility in Baytown.
ExxonMobil and Amcor’s agreement is part of a five-year deal to help Amcor reach its goal of having 30% recycled material across its portfolio by 2030. In July, Amcor and food company Mondelēz announced they were also teaming up on an “advanced recycling” for plastic packaging project in Australia. Amcor and Mondelēz are also among the major companies last year that publicly called for access to up to 800,000 metric tons of chemically recycled plastics by 2030, saying better chemical recycling infrastructure could help them collect the materials they need to meet recycled content commitments.
At the same time, the industry faces uncertainty around possible changes to the Federal Trade Commission’s Green Guides, which dictate how to market environmental claims without being deceptive. Changes to that document could affect how companies will be allowed to claim recycled content that comes from chemical recycling processes. Among the considerations is how companies use mass balance to report the amount of recycled plastic used in an item, and whether the complex calculation is too confusing or misleading to consumers.
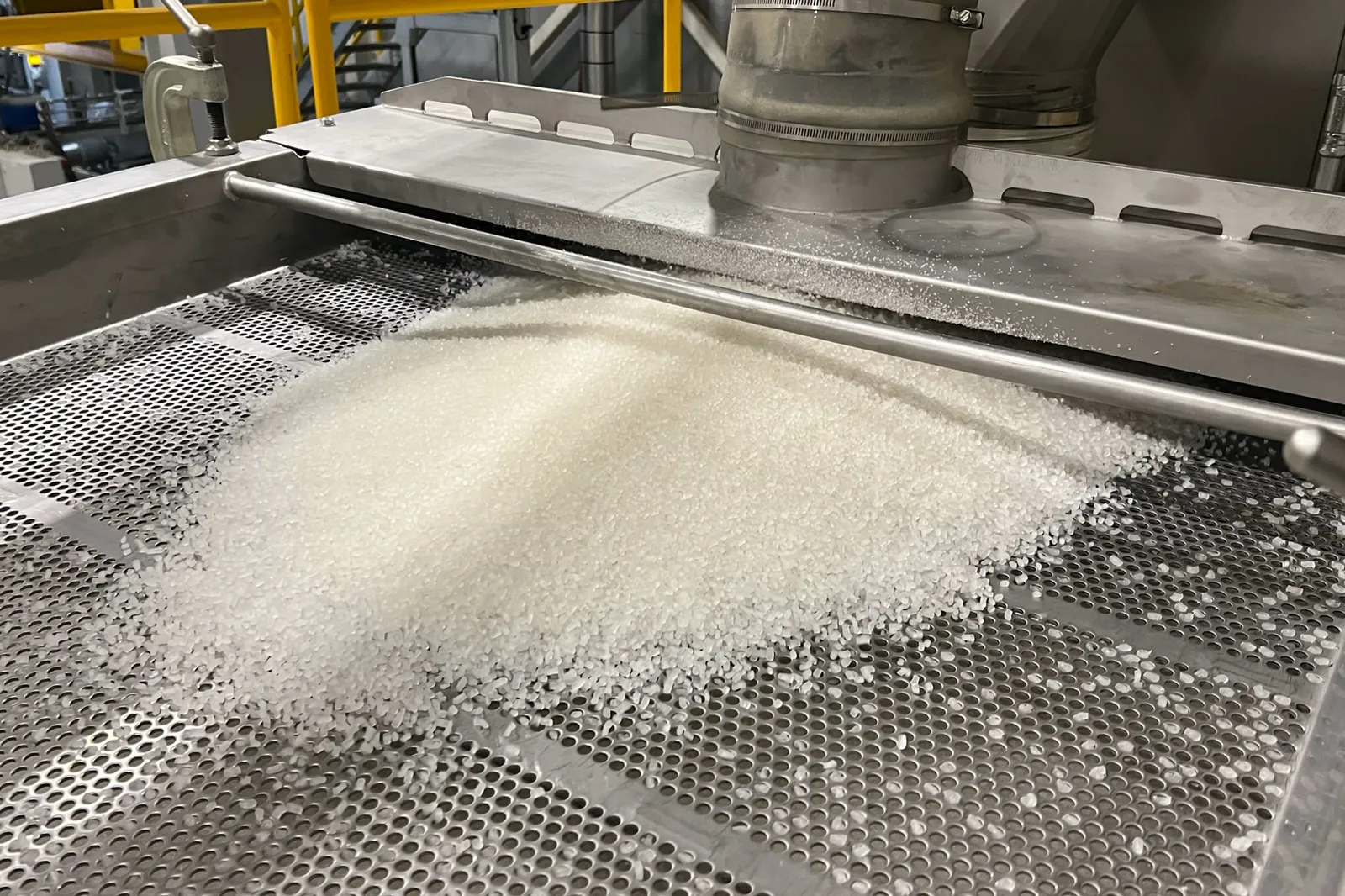
Calls for transparency
Environmental groups have repeatedly called for chemical recyclers to be more transparent with data and information about their operations and environmental impact. Others have also called for a nationwide moratorium on such facilities while more research is done.
The Recycling Partnership in January also called for the chemical recycling industry to be transparent about its operations, including offering more specific details on their technological processes and impact on the climate and surrounding communities.
“Having the technical capability does not necessarily mean there is access to the supply of material,” the organization said in its position statement. “Chemical recycling processes should be driven by a genuine need to turn old plastics into new products with transparent reporting as to what these operations yield. They should not be motivated by a desire to claim that ‘recycling’ is occurring without meaningful production of raw material.”
Back at Rumpke, Snyder said the company’s MRFs are not actively collecting flexible plastic, but there’s enough of it flowing through their facilities to collect a truckload about every five to six weeks.
With the opening of its new MRF later this year, Rumpke says it will have greater flexibility to sort plastics to more precise specifications from all types of customers, meaning it could sort materials for chemical recyclers in the region.
“All those Target bags, those Walmart bags — even though I say I don't want it, we sometimes can grab it, bale it up,” he said. That material might end up being a feedstock for chemical recyclers, said Snyder, along with bulky rigids such as laundry baskets and large cat litter containers.
Despite chemical recyclers’ continued partnership announcements for offtake agreements and deals with plastics recyclers and other feedstock providers, the unknowns about such facilities’ impacts still loom large, said Lynn Hoffman, national coordinator for the Alliance of Mission-Based Recyclers. Too little is known about where chemical recyclers are sourcing their materials, what exactly they’re creating with them and what the real impact of that technology is, she said during a December webinar about chemical recycling’s impacts.
“What's missing so far are those important transparent metrics. What are the inputs? What are the outputs and what are the actual impacts?” Hoffman said. “They've got a good sales pitch, I guess is what I would say.”