Casella Waste Systems recently reopened its Boston MRF after a complex upgrade process that packed more capabilities into a tight footprint.
The $20 million project, led by Machinex, expanded capacity at what the company says is the largest MRF on the East Coast and the fourth-largest in the United States. Casella’s biggest MRF now has more operating flexibility, new artificial intelligence and sorting capabilities, cleaner commodities and a lower headcount.
Maximizing space was important given the project’s location in Boston’s Charlestown neighborhood. The facility sits in a small industrial park alongside a major highway, multiple rail transit lines, a community college, a growing mixed-use development and other businesses. The company runs a separate commercial recycling facility on the same road as the updated residential MRF, with a long-time fruit and produce wholesaler in between.
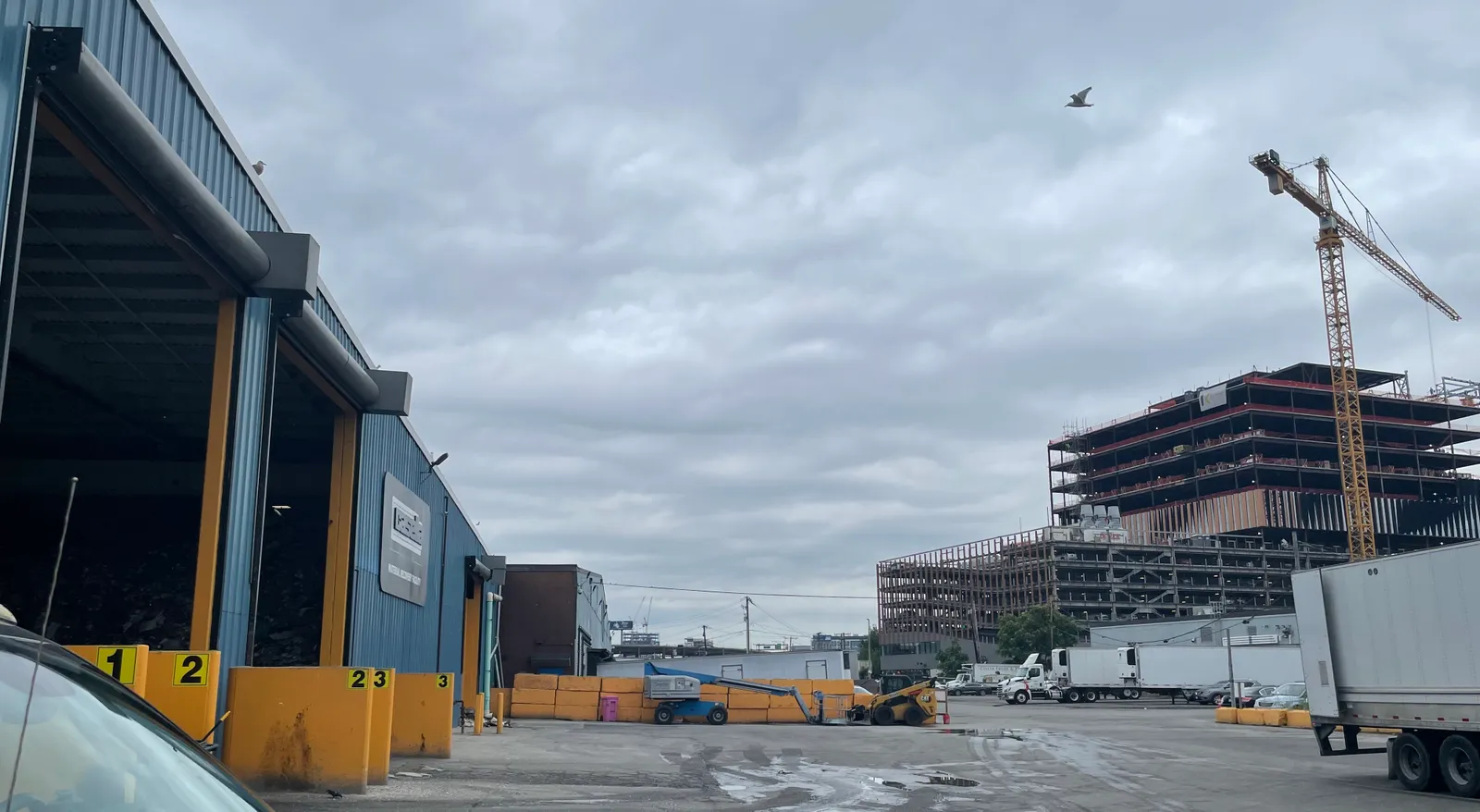
Bob Cappadona, vice president of resource solutions, said during a recent tour that it took "tremendous engineering on the Machinex side just to fit everything in the building.” Aside from two optical sorters and a couple small scalping screens, almost everything was replaced with new equipment.
The updated design increased tip floor capacity from an estimated 500 tons to up to 1,500 tons. The system also now has three balers, up from two, with new reversible transfer belts that allow for more flexibility if one unit goes down.
The decades-old Boston MRF has seen multiple updates during its lifespan. Casella picked up the facility during its 1999 acquisition of KTI Recycling, which had previously acquired it from Prins Recycling via a bankruptcy process. Casella made its last major upgrade to the facility in 2009 when it converted it to run as a single-stream system. Sherbrooke and CP Manufacturing led that project.
Cappadona said the design had become “antiquated,” after lasting the expected lifespan of 10-15 years, and an update was in order. Casella estimates it processed nearly 3 million tons of material there since 2009.
Casella experienced a roughly eight-month supply chain delay for equipment, leading it to begin the project early this year. It shut down the facility for an estimated 20 weeks at a time when volumes are typically lower. Casella shifted an estimated 75% of material to other recycling facilities it runs in Massachusetts, Connecticut and Maine during the process.
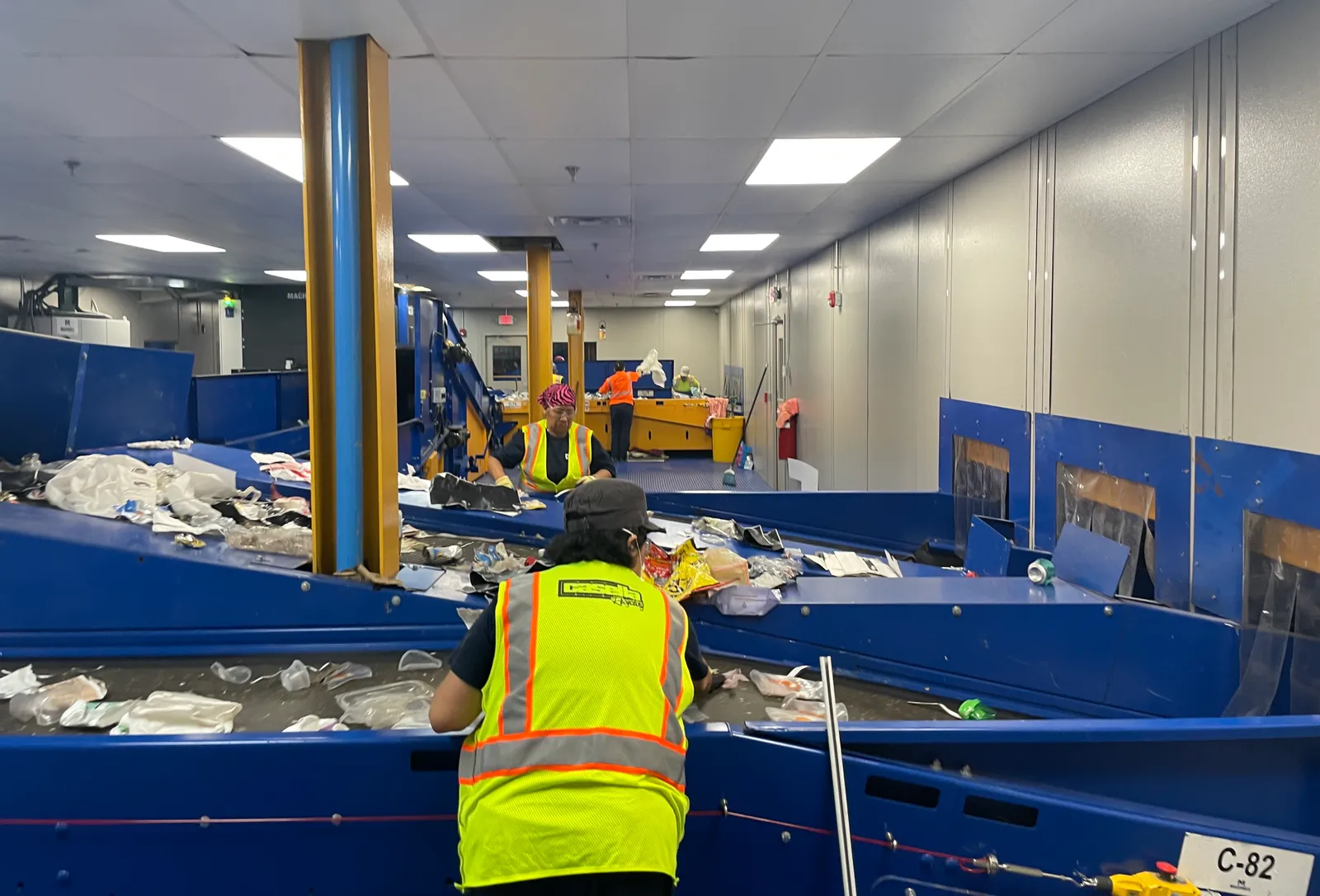
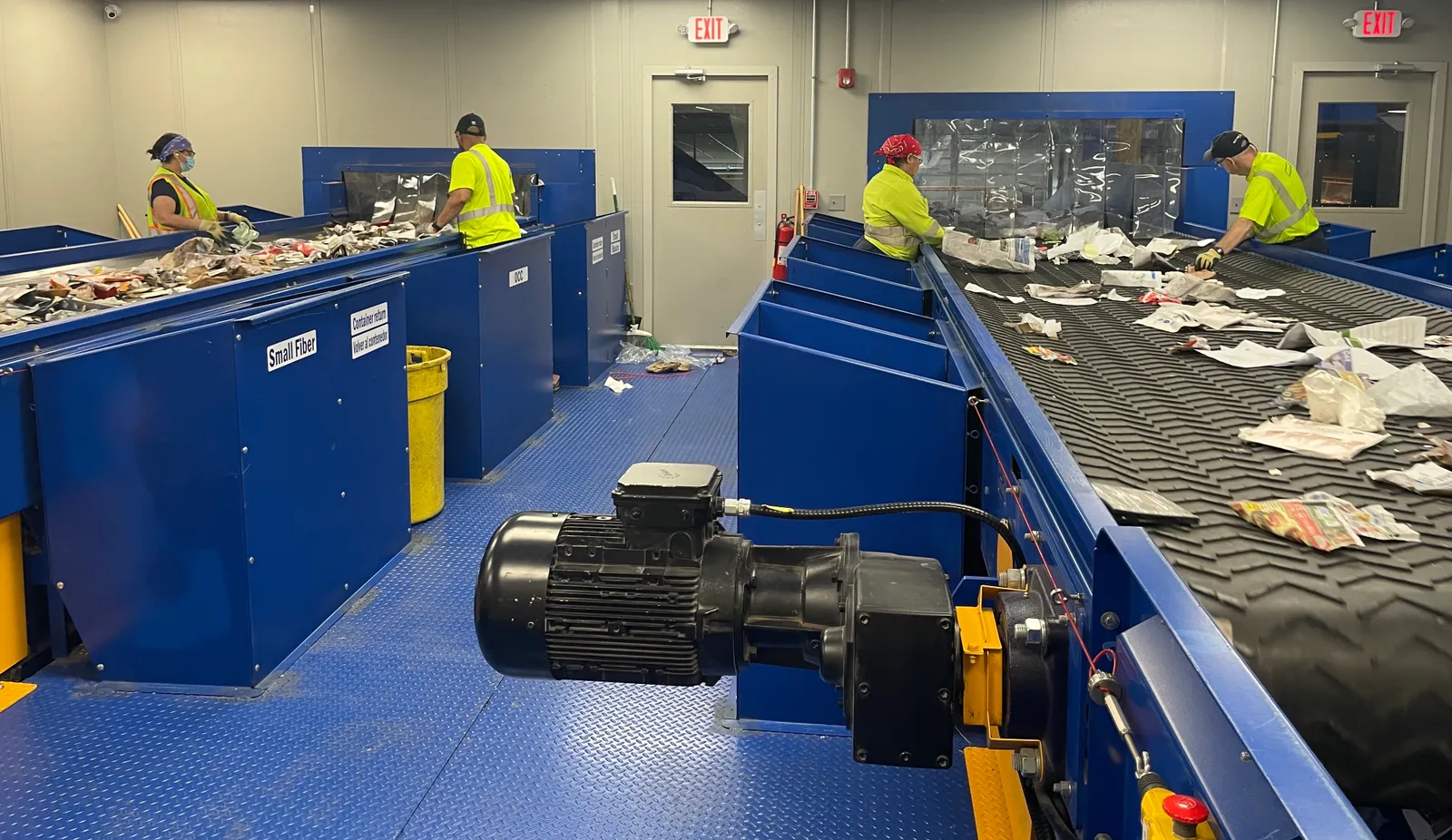
Cappadona touted multiple benefits of the revamped operation, including enclosed work stations for sorters that can improve safety, a complex serpentine-like design that maximizes use of the space and various improvements to capture more value from the stream.
In addition to the nine optical sorters and two scalping screens, the system has two ballistic separators, various aspiration points to remove film (plastic bags remain the top contaminant despite various local ordinances meant to limit them) and multiple magnets, among other features.
Casella said the optical sorters’ new stacked design allows for better separation and throughput on the fiber segment to produce a cleaner news grade. A new glass processing system could also result in higher value in the future.
Massachusetts bans glass from disposal, but the 2018 closure of an Ardagh bottling facility has limited the local options. Glass from Casella’s Boston facility is now primarily used for construction or road applications. The new system can process glass into a 2-inch size for bottle markets, and a 3/8-inch size for markets such as foam aggregate to be used as stone replacement or as an additive in the cement market.
"It will give us the flexibility of going to different markets, when a market comes up here,” said Cappadona, adding that the company could pivot relatively quickly to “upgrade to a cleaner product.”
Similarly, he said the vacuum system for plastic bags means Casella could make a slight adjustment to capture that stream as a commodity “if a market ever comes to fruition.”
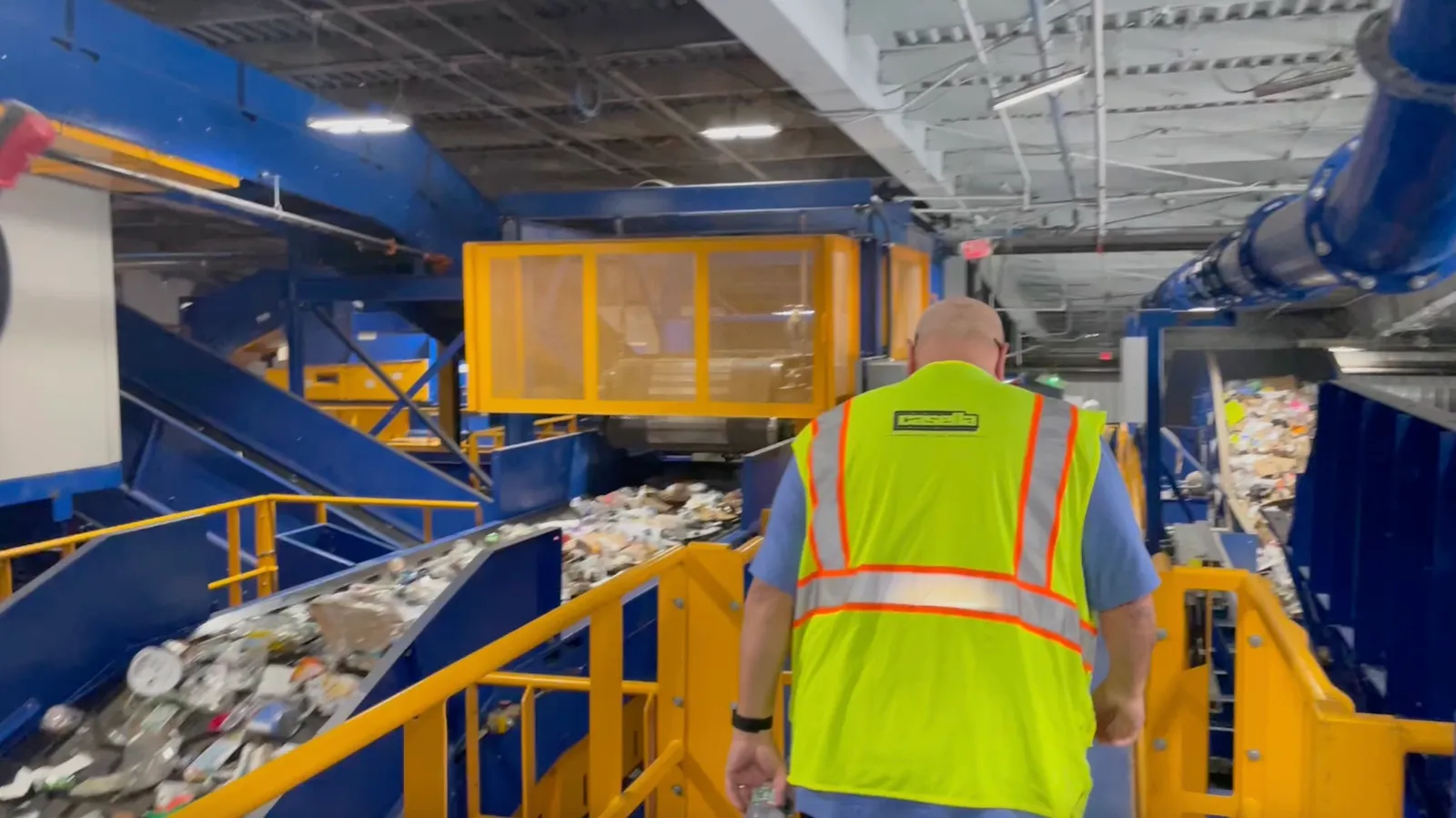
Casella says the addition of Machinex’s SamurAI technology, located at the end of the system, can also increase value by catching anything the opticals may have missed. Jeff Weld, Casella’s director of communications, said this allows the system to adjust “on the fly” and gain insight into the percentage of certain materials passing through parts of the system.
Cappadona said the new capacity allows for future contract expansion in the area as municipalities look to grow their recycling volumes and positions Casella to continue its longstanding presence in the Boston market.
Today the facility receives material from approximately 75 municipalities in the area — including a mix of direct haul, third-party and intercompany volumes. The city of Boston is its largest customer through a residential processing contract. Material comes from as far as New Hampshire, which sends an estimated 30,000 tons per year.
The Vermont-based company said it has spent more than $30 million on other recycling-related projects in recent years and further growth is underway.
After surpassing $1 billion in revenue last year, Casella completed a major Mid-Atlantic expansion with the recent $525 million purchase of assets from GFL Environmental in Delaware, Maryland and Pennsylvania. It also recently announced the pending acquisition of New York’s Twin Bridges Waste & Recycling for an estimated $219 million.
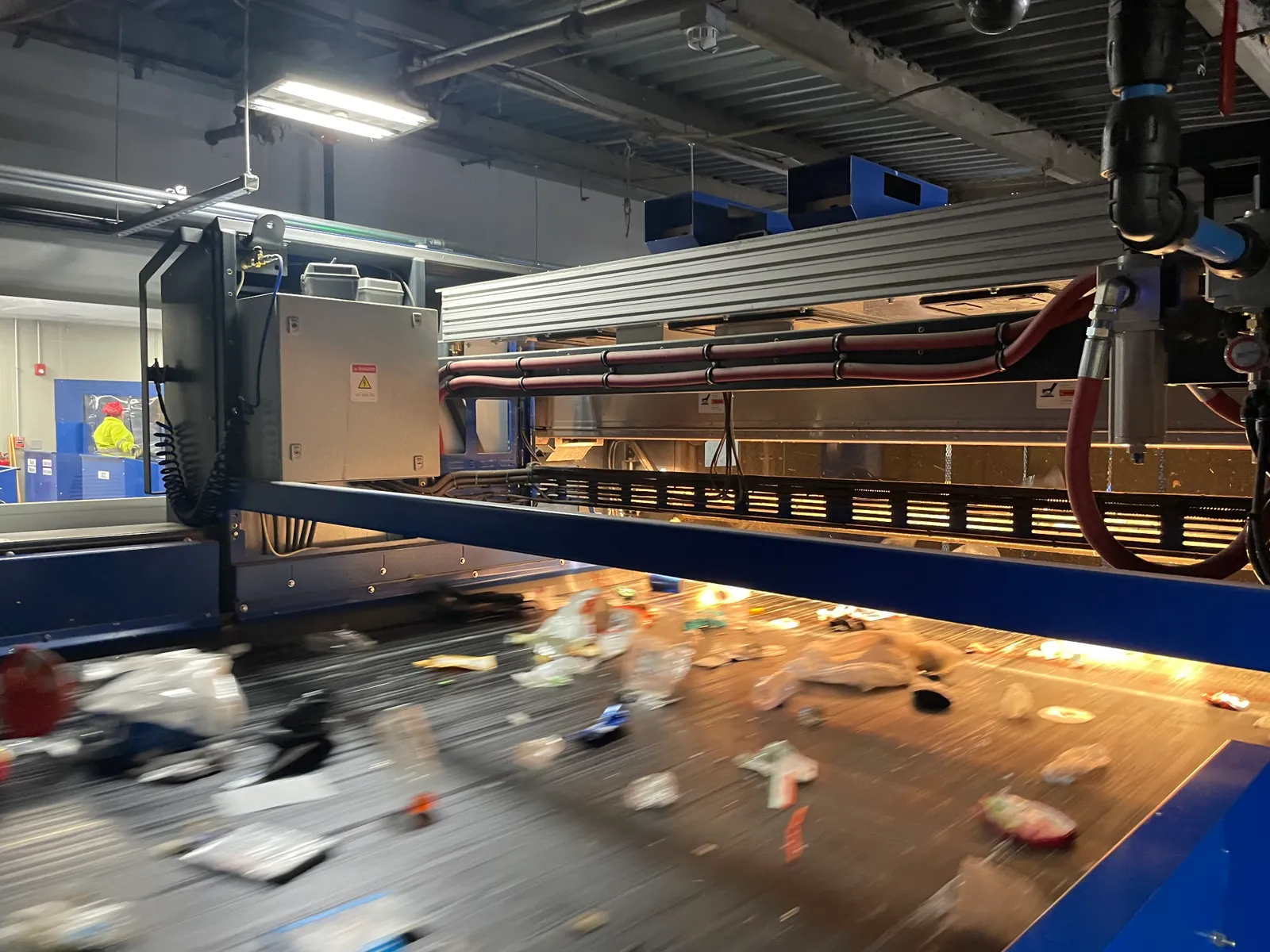
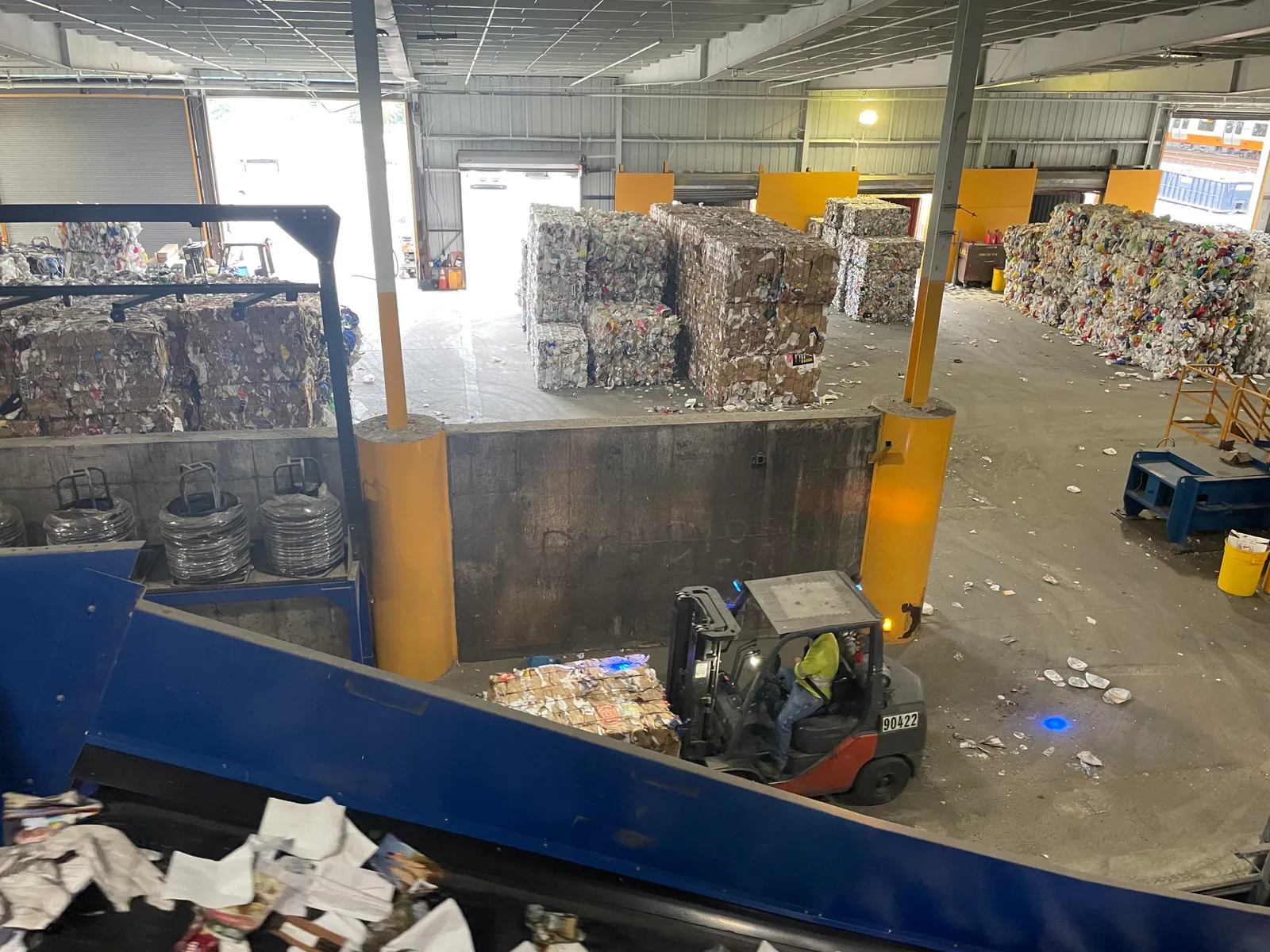